Blog
11.272019
生産管理の見える化の目的と進め方のポイント
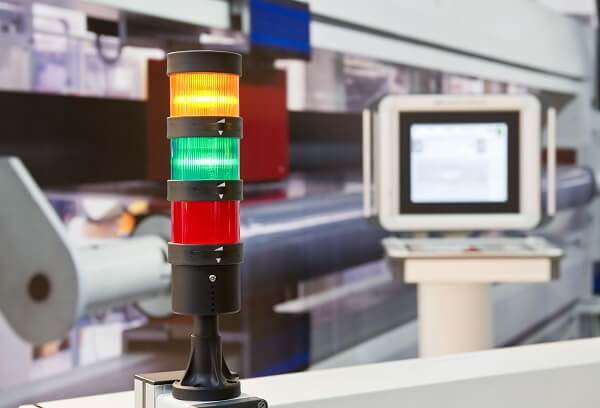
見える化で生産管理の7大弊害をなくす
生産現場では、様々なものが「見えない」ことにより、計画通りに事が進まない、生産高が上がらない、利益が出ない、顧客に迷惑をかける、従業員が辞めてしまうなど様々なムリ・ムダ・ムラの問題が生まれます。
生産管理では、モノ、4M、QCDS、情報、日常管理、方向性と思い、全体および経営という7つの視点から見える化を進めることで、これら問題を解決することができます。
ここでは、生産管理の見える化の目的と役割について解説します。
<目次>
見える化の目的とは「結果をつくるマネジメント」の実現
見える化によって行動を管理する
生産管理における見える化のねらい
生産管理における見える化の役割
7つの視点で見える化を進める
見える化の目的とは「結果をつくるマネジメント」の実現
見える化によって結果基点の管理から脱却する。
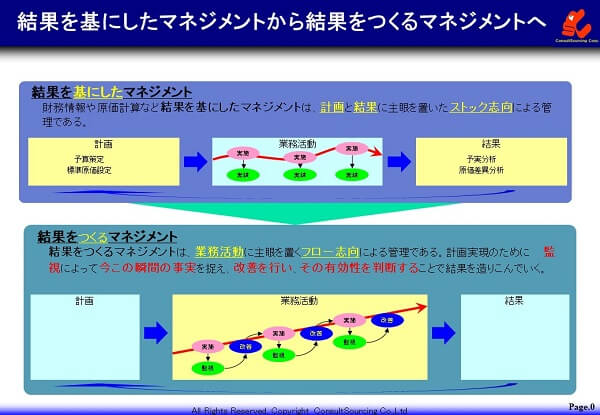
結果を基にしたマネジメントとは
月初または年度初めに立てた計画は、月末または年度末に結果として現れます。
目標とした数値に対し、達成したのか未達なのか結果を管理ます。
このような計画と結果に主眼を置いたストック志向の管理が、結果を基にしたマネジメントです。
結果基点の管理では、例えば、予実差異が結果として発生した時、「大幅な仕様変更があったからなのか?」、「新人が配属されたなのか?」、「部品の不良が多かったなのか?」などどれも推測にすぎなくなってしまいます。
よく「見える化」というと「今月の不良件数は何件であった」、「生産実績はこうだった」など結果の数値をグラフや一覧できれいに並べ、それを見ながら良かった/悪かったと一喜一憂することが多く見られます。しかしながら、このようなスタイルは、過去の管理と言わざるを得ません。
めざすのは結果をつくるマネジメント
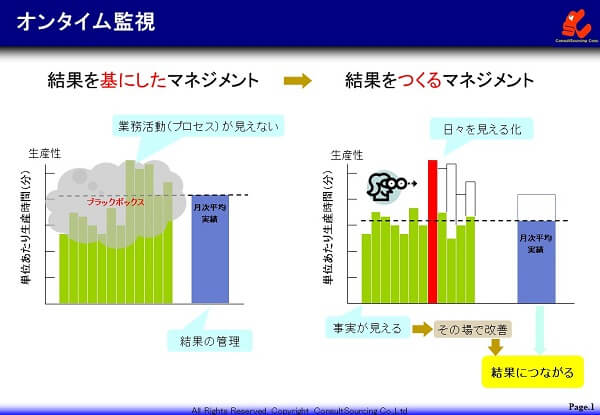
月初または年度初めに立てた計画を結果に結び付けるには、月中の業務活動が重要です。
刻々と変化する業務活動の事実を瞬間で捉えその場で改善を行いその有効性を判断することで、良い結果に導かれます。
このような業務活動に主眼を置いたフロー志向の管理が、結果をつくるマネジメントです。
つまり、見える化は、業務活動というプロセスの日々を見える化しオンタイム監視することで、「仕様変更があったので悪かった」、「新人が配属されたので生産性が落ちた」、「設備不良があったので稼働時間が少なくなった」というようなことが分かり、改善が促されます。
日々改善でそれぞれの問題が処置されれば、それが月末の結果として未来の数値につながります。
グラフや一覧できれいに見せることよりも、監督者や作業者の行動を促すような今の見える化をし、PDCAサイクルを回し、今を管理することが大切です。
見える化によって行動を管理する
管理項目には、結果系の管理項目と要因系の管理項目があります。
結果をつくるマネジメントは、要因系の管理項目を見える化し、行動を変えることにあります。
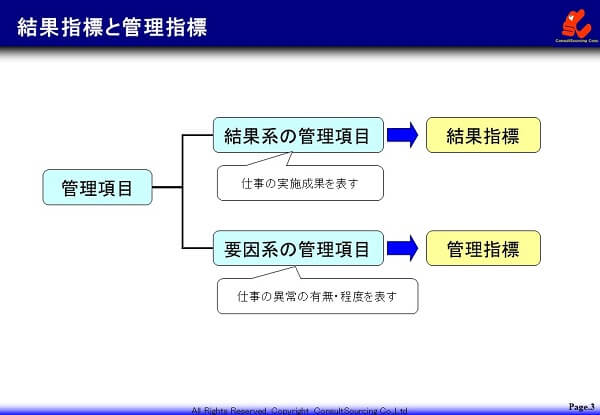
結果指標とは
経営や管理において、めざす姿や目的が設定されています。
そこから経営方針に沿って部門目標に落とされ、最終的に企業や組織が求める結果を判断する項目が、結果系管理項目となります。
つまり、いつまでに、何を、どの程度にするかを明確にしたものです。
このとき、「何を」に相当するものが、結果指標となります。
例えば、「総時間あたりの生産高」、「流出不良」といった結果指標を決めて、測定や監視を行い、適切な状態から外れたときに対処できるようにします。
管理指標とは
月末や年度末にこうなっていたいという結果指標を実現するためには、実施する施策や具体的な業務活動が必要となります。
つまり、結果をつくるマネジメントに必要な行動 (プロセス)を明確にします。
例えば、総時間あたりの生産高を高めたいといった結果指標に対しては、「不良・手直しロスの削減」や「動作ロスの削減」というような、具体的行動を洗い出します。
その実施すべき行動の適正性を具体的に示したものが要因系管理項目になります。
つまり、いつまでに、何を、どの程度になっていることが、適正なのかを明確にしたものです。
このとき、「何を」に相当するのが管理指標となります。
例えば、上記例では、「不良・手直し回数やロス時間」や「動作ロス時間」が管理指標となります。
結果をつくるマネジメントでは、このような管理指標を使って管理をします。
結果指標で示された目標は、努力しても、環境変化や自分たちを上回る競合などにより、求める結果が得られないこともあります。
ですから、結果指標で管理しても、自分たち以外の要因で結果が左右されてしまうため、適切な管理ができません。
一方、管理指標で示された目標は、人の意識と行動によって、達成の程度を操作することができます。
人の意識や行動によって左右されるのが管理指標ですから、人の意識や行動の適正性を評価し管理することに適しています。
見える化して行動を管理する
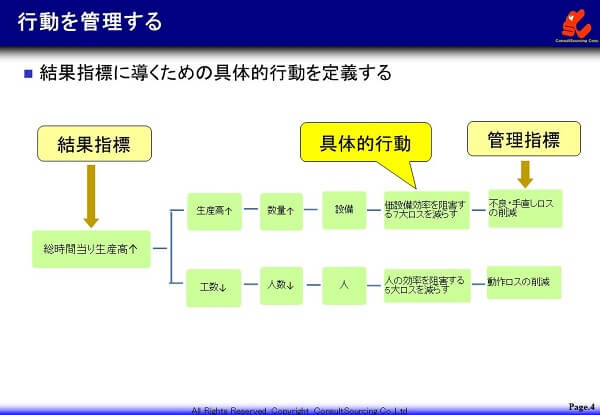
要因系の管理項目である管理指標は、結果を生み出す基となる施策や行動の適正性を判断する項目です。
仕事の実施上の異常の有無や程度を判断するもので、行動指標とも言います。
管理指標は、その行動が、求める結果を導き出すことに貢献する適正なものとなっているか、測定・監視するモノサシですので、管理指標で今を見える化し、正しい行動が増えていれば、自ずと結果指標につながることになります。
生産管理における見える化のねらい
見えることで行動が生まれるようにします。
見えるようにすることで、生産管理・製造現場において、今、何をすべきかを示します。
見える化で行動を開始させる
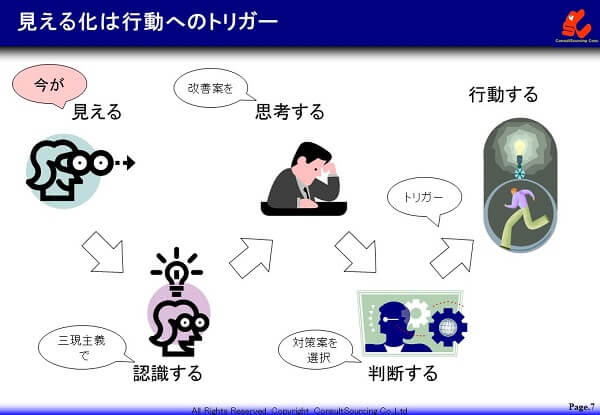
何も見えない状態では、暗中模索で何をしたらよいか判断がつきません。
見えないものが見えるようになることで机上ではなく三現主義に即して、
・現地(現地に行ってモノを見る)
・現物(現物を手にしてモノを確認する)
・現認(現実を目で見て事実を認知する)
という視点で、改善案を考え(思考し)、対策案を選択(判断)し、行動(改善)が生まれてきます。
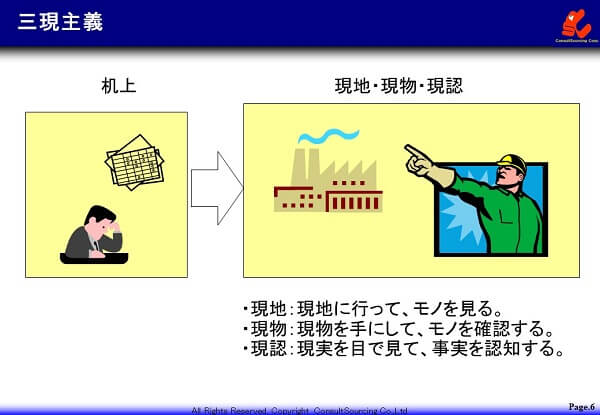
つまり、見える化は行動に結びつけるためのトリガーと言えます。
トリガーとは引金(銃などを操作するスイッチ)のことで、きっかけづくりの役割を果たします。
そして、「見える→認識する→思考する→判断する→行動する」という一連の連鎖を通じて、ムダが見顕在化し、改善ニーズとなり、改善行動となり、ムダの排除につながります。
見える化で知識を行動に変える
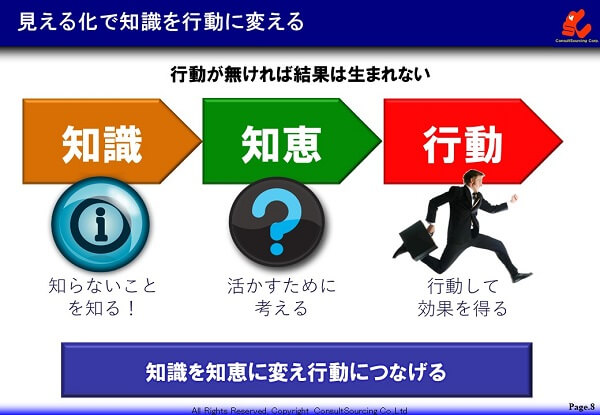
世の中情報が溢れ、分からないことがあればすぐにネット検索で知識が得られるようになってます。
しかしながら、どんなに知識を沢山持ち合わせていても、それが自社に活用できるような知恵に変わり、実際の行動につながらなければ、知識の持ち腐れになってしまいます。
行動がなければ何の結果も生みません。行動に変えるためのツールが、見える化となります。
見える化で人づくり
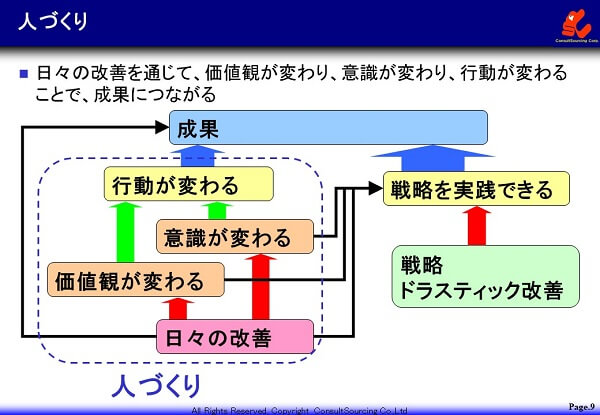
見える化から日々の改善というプロセスを通じて、人は変化していきます。
見えなかったから動かなかった従前から、見えることで何とかしなければいけないという価値観に変わります。
そこから当事者意識が沸き、自律的に何かしようという意識に変わります。
意識が変われば、行動が変わっていきます。
このような行動できる人を複数育てていけば、戦略も実践可能となり徐々に組織や組織風土が変わり、成果となっていきます。
生産管理における見える化の役割
見える化の役割は管理・改善の基盤を構築することにあります。
マネジメントと氷山の関係
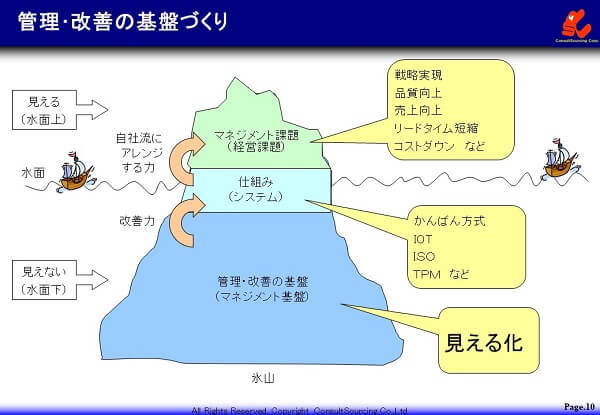
企業には、戦略実現・品質向上・売上向上・リードタイムの短縮・コストダウンなどの様々なマネジメント課題(経営課題)が存在します。
これらは氷山で言えば水面上にある見える(認識できる)課題であり、それらを解決すために各企業は仕組み(システム)を構築し、課題解決に向けた取り組みを行います。
しかし、それらの仕組みを導入した企業が必ずしも成果を出しているとは限りません。
例えば、かんばん方式を形だけ真似してもそれが現品票の役割にしか使われず、
ジャスト・イン・タイムどころか原価低減に一切寄与していないケースも多々あります。
昨今のIOT(モノのインターネット、Internet of Things)でも、異常サインが出てもどうしたらよいか分からず何も行動しないようなことも起こります。
世間で流行していたり、話題となっていたりする様々な仕組み(システム)を単に導入し、成功している企業と同じやり方を真似しても、自社の企業風土・習慣・文化が異なるため、自社流にアレンジできず課題解決には至りません。
一方で、氷山には目に見えない水面下の部分がかなりあります。
仕組みを上手に動かし課題解決を図りたいのであればこの水面下に着目する必要があります。
これが管理・改善の基盤(マネジメント基盤)と言われるものです。
この基盤がなければ、他社の優れた仕組みや基本的なパッケージを改善し、自社のDNAと融合することはできません。
基盤ができてはじめて仕組みがまわり、マネジメント課題が達成できます。
見える化によって管理・改善の基盤をつくりあげる
管理・改善の基盤は、様々な卓越した仕組み(システム)を環境がめまぐるしく変わる中、常に状況対応させていくためのベースです。
このような土台(ベース)が弱ければ、その上に乗る仕組み(システム)も機能しないし、マネジメント課題も解決されません。
この管理・改善の基盤を、見える化をツールとして構築し、仕組み(システム)を自社流にアレンジすることで、種々のマネジメント課題が達成されていきます。

7つの視点で見える化を進める
生産現場には見えない7つの弊害があり、見える化によってこれら弊害をなくします。
見えないとはどのようなことで、どのような弊害をもたらすのでしょうか。
モノが見えない弊害
製造現場における物理的なモノ、例えば、材料・製品・仕掛品・不良品・工具・治具などが見えない状況下では、探す、手待ち、つくり過ぎ、不良品流出などの弊害を生みます。
4Mが見えない弊害
Man、Machine、Method、Materialが見えない状況下では、ムリ(過度の負担)、ムラ(バラツキ)、ムダ(付加価値を生まないこと)などの弊害を生みます。
QCDSが見えない弊害
Quality、Cost、Delivery、Safetyが見えない状況下では、不良増加、コストアップ、納期遅れ、重大事故などの弊害を生みます。
情報が見えない弊害
開発・購買・生産・運搬・引き取り・販売などに関する様々な情報が見えない状況下では、生産状況が把握できない、生産計画の混乱、欠品、誤配送、誤った図面でモノを生産してしまうなどの弊害を生みます。
日常管理が見えない弊害
生産管理・購買管理・在庫管理・工程管理・品質管理・設備管理・原価管理・安全管理・労務管理などの日常管理が見えない状況下では、要員管理や設備に関する負荷・能力も調整できない、在庫・死蔵品の発生、ライン停止などの弊害を生みます。
方向性および思いが見えない弊害
様々な組織、階層、部門、国籍、年齢、男女、関連会社などが共存する中、方向性や思いが見えない状況下では、お互いのベクトルが合わずバラバラな動きになり、もぐらたたきの場当たり的な行動になってしまうなどの弊害を生みます。
全体および経営が見えない
自分の周囲のことしか見えない状況下では、自分(自工程)さえよければよい、部分最適に終始し工場全体が見えない、自分の努力が経営に反映されているのか見えずモチベーションが上がらない、経営者の意思が伝わらない、会社(自分)の将来に不安を覚えるなどの弊害を生みます。
Copyright © 改善と人材育成のコンサルソーシング株式会社