Blog
2.72019
品質管理とは~基本知識と品質管理の3つの管理業務の内容
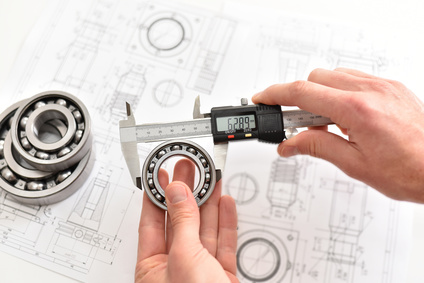
品質をつくり込み検査して保証する品質管理の進め方
品質管理は、工程管理、品質検査、品質改善の3つの取り組みを通じた管理です。
3つの管理によって、工程の中で、品質がつくり込まれ、品質が確かなものであることを検査で検証し保証することです。
品質管理とはどのようなもので、工程を管理し、品質を検証し、品質の改善を行うための基礎知識と業務内容を紹介します。
<目次>
品質管理とは
品質管理の3つの管理
工程管理の方法とその効果
品質検証の方法とその効果
・検査の基礎知識
品質改善の方法とその効果
品質管理とは
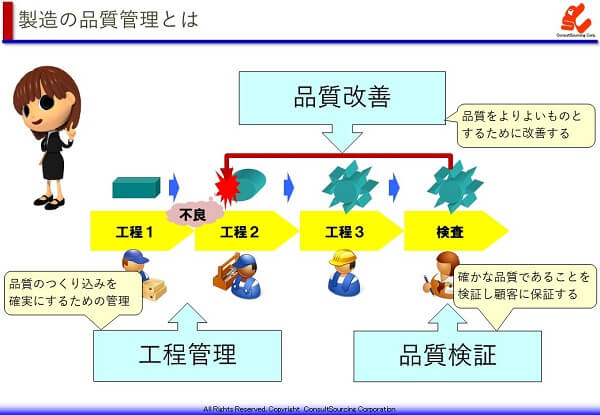
製品は、一連の工程を経て製造され、検査で品質を確認して完成します。
品質管理は、このような製造の中で、品質がつくり込まれ、品質が確かなものであることを検査で検証し、保証することです。
品質管理では、3つの管理を通じて、製品品質を保証します。
工程管理は、品質をつくり込むために、工程を適切な状態に管理します。
品質の検証は、検査などによって、製品や工程が確かなものであることを検証し、保証します。
品質改善は、不適合の再発防止、未然防止のための改善を行います。
ちなみに、品質管理の世界では、不良、不合格などのことを不適合と言います。
不良品、不合格品は、不適合品となります。
品質管理の3つの管理
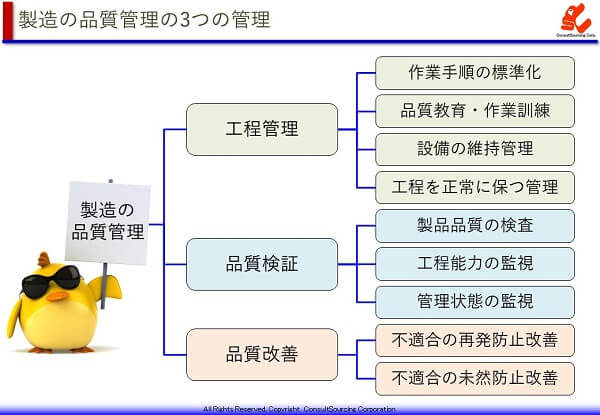
それでは、品質管理の3つの管理は、どのような管理をするのか見ていきましょう。
工程管理では、確かな手順で仕事がされるように作業手順の標準化をします。
確かな品質をつくり込める人を育成するための教育訓練を行います。
設備能力を維持するための管理を行います。
工程が、常に正常な状態に保たれるように管理します。
品質検証では、まず、製品が確かなものであることを検査します。
工程も品質をつくり込む能力を維持しているか監視します。
工程管理や検査などが適切に実施されているか監視します。
品質改善では、発生した不適合の再発防止のための改善をします。
また、将来発生するかもしれない不適合の未然防止のための改善もします。
それでは、それぞれの管理が具体的にどのように行われ、どのような効果があるか見ていきましょう。
工程管理の方法とその効果
最初は、工程管理の方法とその効果です。
作業手順の標準化
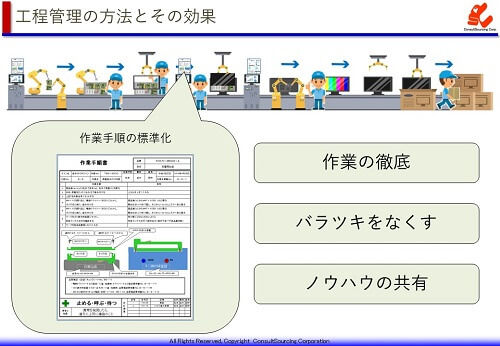
作業手順の標準化は、品質をつくり込むための適切な手順を標準として定め、作業手順書などに表すことです。
作業手順書によって、周知し、教育することで、品質をつくり込むための正しい作業を徹底することができます。
作業手順書によって作業手順が統一されることで、人による違い、つくるタイミングによる違いなどが無くなり、品質のバラツキが無くなります。
バラツキが無くなることで、何か異常が発生したときに、すぐに気づくことができ、不適合となる前に処置することができるようになります。
品質を高めるための改善案やノウハウを作業手順書に反映することで、作業する人たち全員と共有をすることができ、職場全体の品質のつくり込み力が高まります。
品質教育と作業訓練
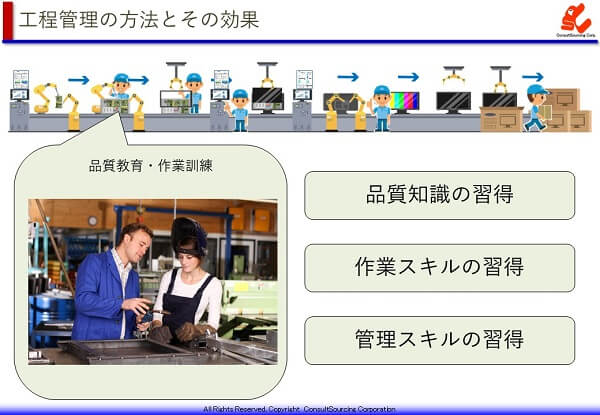
品質教育、作業訓練は、品質をつくり込み、管理するために必要な知識と技能を習得するための研修やOJTを行います。
OJTとは、仕事を通じて行うトレーニングのことを言います。
研修などの教育では、製品や工程、設備、作業方法など、品質知識の習得を行います。
OJTなどの訓練では、品質をつくり込むための技能を高めます。
技能とは、腕前と言われるような、作業を高いレベルでできる力のことを言います。
管理スキルとは、品質を適切に管理するための知識や技能のことを言います。
研修や改善経験を通じて習得します。
設備の維持管理
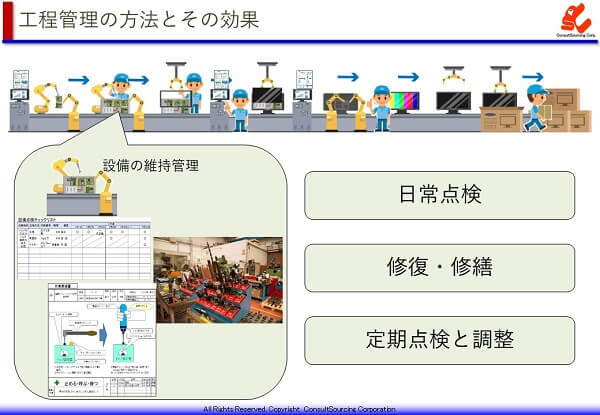
設備の維持管理は、日常点検などを通じて、設備異常を早期に発見し、不適合品の発生を検知したり、未然防止をはかったりします。
加工用の刃物や型、冶具などの摩耗や劣化した箇所を修繕したり、交換したりすることで、生産が、常に適切な状態で行われるようにします。
設備の生産条件や設定値などのズレなどを確認して、設備能力が規定を満たしているか確認し、調整します。
工程を正常に保つ管理
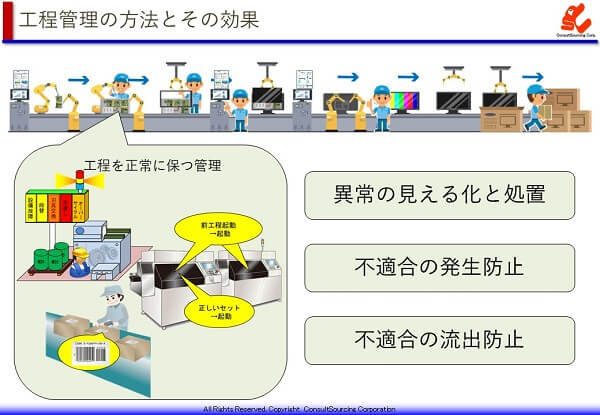
工程を正常に保つ管理では、アンドンなどによって、日々の生産で発生する異常を見える化して、処置することで、不適合の発生を未然に防ぎます。
設備や冶具に、ポカヨケやインターロックなどの仕掛けを組み込むことで、作業ミスや工程飛びなどを防止して、不適合の発生防止をはかります。
工程内での品質確認作業をシステム化することで、不適合を見落として後工程や顧客へ流出させてしまうことを防止します。
熱処理工程における品質管理方法については以下の記事で解説中。
鋳造・ダイカスト工程における品質管理方法については以下の記事で解説中。
鍛造・プレス工程における品質管理方法については以下の記事で解説中。
溶接・スポット溶接における品質管理方法については以下の記事で解説中。
品質検証の方法とその効果
続いて、品質検証の方法とその効果です。
製品品質の検査
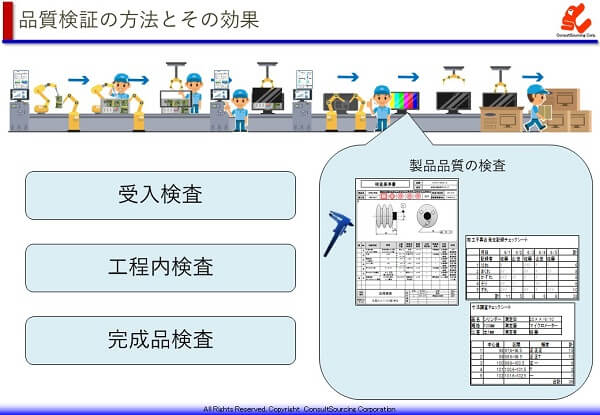
製品品質の検査には、外部から購入した原材料や部品などを受け入れ時に検査する受入検査があります。
受け入れ品の品質を確認して、確かなモノだけを工程に投入することで、不適合の発生を防止します。
製造工程の途中で行う工程内検査もあります。
不適合発生のリスクが高い工程や、完成後では品質確認のできない工程などに限って実施されます。
最終的にできあがった製品の品質を検証し、顧客に品質を保証するために完成品検査をします。出荷に先立って行われることから出荷検査と呼ばれることもあります。
検査の基礎知識
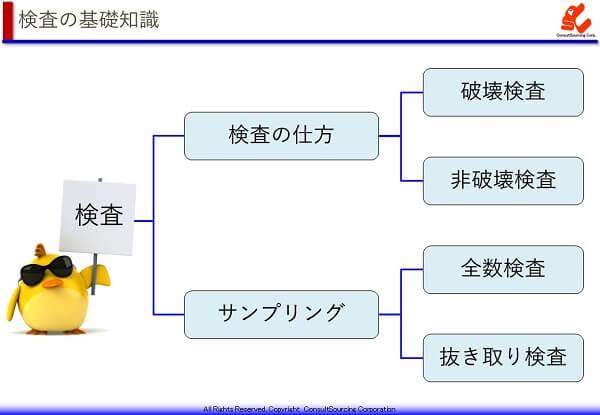
ここで、検査についての基礎知識を紹介しましょう。
検査の仕方には、2種類の方法があります。
破壊検査は、その名の通り、破壊して検査する方法です。
強度や摩耗性など、検査サンプルを破壊しないと調べられないような特性の検査です。
破壊検査が必要となる場合は、検査用のサンプルを余分に生産して、用意しなければなりません。
非破壊検査は、寸法測定など、検査サンプルを破壊しなくても調べられる特性の検査です。
検査サンプルは、製品として出荷できますから、余分に生産する必要はありません。
検査サンプルの抽出、つまり、サンプリングも2つの方法があります。
全数検査は、生産した製品のすべてを検査対象とする方法です。
出荷品の全数を検査しなければならない要求がある場合、工程が安定しない場合、統計的に工程能力が評価できない場合などに採用される方法です。
抜き取り検査は、生産したロットの中から、検査に必要な分だけ抜き取って検査する方法です。
抜き取り検査は、工程が安定し、工程能力指数などによって工程能力の検証ができているラインで生産されたモノに対して行うことができます。
また、破壊検査など、全数検査ができない場合にも行われます。
抜き取り検査は、経済合理性に照らして、顧客側も不適合品を受け取る可能性があることを認識している場合に行われます。
工程能力の監視
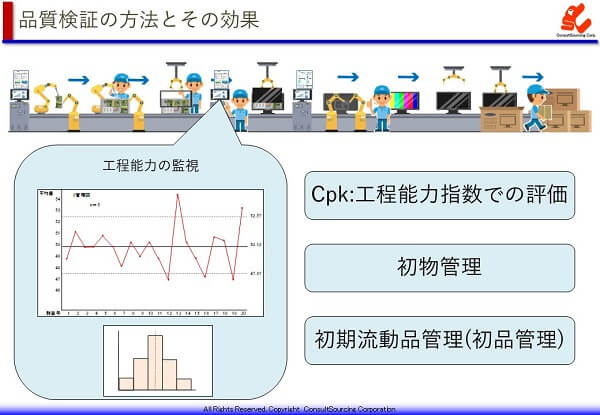
工程能力の監視は、工程が品質をつくり込むために必要とされる能力を有しているか確認・監視することです。
工程能力の監視には、CpまたはCpkと言われる工程能力指数などを算出して、評価する方法があります。
生産した製品の一定量を測定して、統計処理し、不適合の発生確率を推定する指標で、量産品などの品質管理で広く取り入れられている方法です。
初物管理は、ラインで生産する製品の切り替えなどによって、材料、刃物や型、製造条件などを変更したり、準備・段取りしたりした後、最初に生産したモノの品質をチェックして、正しく準備・段取りされたか確認することです。
初期流動品管理は、新製品などの量産初期の品質管理を厳しく行うものです。
新製品は、工程が不安定であったり、作業者や検査員の習熟度も高まっていなかったりするため、不適合が発生するリスクが高くなります。
そこで、工程内での確認や検査の頻度、項目を増やして、不適合の流出防止と品質改善を行います。
管理状態の監視
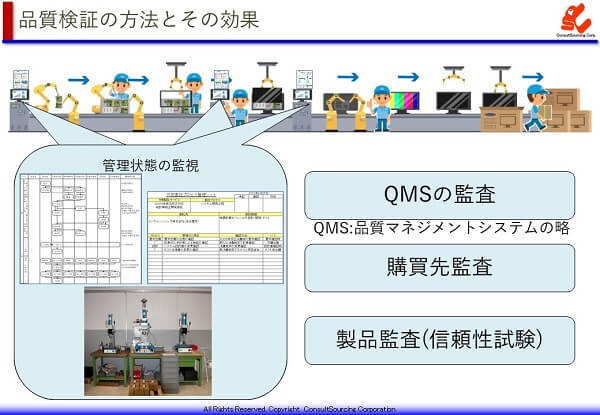
管理状態の監視は、品質マネジメントシステムが正しく運用され、必要とする管理が適切に行われているか、監査などを通じて確認・監視します。
ISO9000などの品質システム監査などが該当します。
材料や部品を購入している購買先でも、品質マネジメントシステムが正しく運用されているか確認するために、購買先監査なども行います。
購買先がISO9000などの認証を取得している場合は、購買先監査を省く場合もあります。
耐久性や経年劣化など日々の検査では検証できない品質特性などについて、信頼性試験などを行い、確認する製品監査も実施します。
耐久性や経年劣化などの品質は、日々の品質管理によって保証されていますが、その裏付けを取ることが製品監査の目的です。
品質改善の方法とその効果
最後は、品質改善の方法とその効果です。
不適合の再発防止
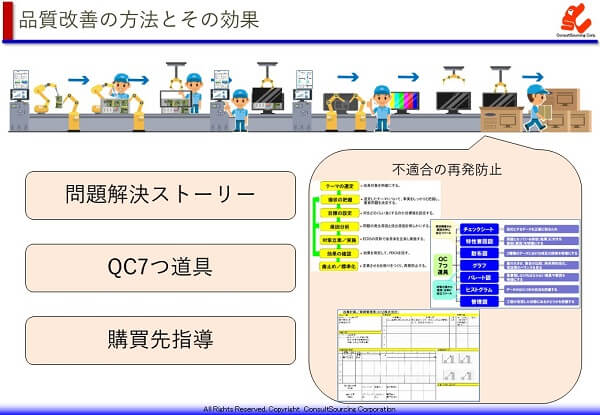
不適合の再発防止のための改善は、問題解決ストーリーと言われる、現状の把握、原因の分析、対策立案など、問題解決のための一連のステップに基づいて行います。
原因を究明し、発生原因を取り除いて、不適合が発生しないようにします。
品質改善では、すべては事実に基づいて改善を行います。
事実を裏付けるデータを収集し、分析して、評価するために、QC7つ道具などの統計的手法を使います。
品質改善は、自社だけでなく、原材料や部品の購入先にも、その実施を求めていきます。
不適合を発生させた購買先には、再発防止のための品質改善を強く求め、改善の指導を行います。
不適合の未然防止
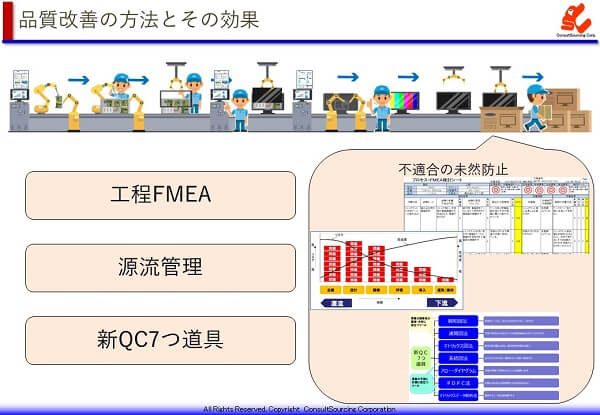
不適合の未然防止の代表的手法の1つが工程FMEAです。
Failure Mode and Effect Analysisの略で、故障モード、影響解析という意味です。
製造工程における様々な潜在的トラブルの洗い出し、未然防止の改善をします。
変化点管理と組み合わせた工程FMEAの手法も広く使われています。
源流管理は、その名の通り、源流、つまり、上流にさかのぼって管理する方法です。
製造の源流は、生産準備と言われる生産ラインの設計、構築段階です。
さらに、その上流は、製品の開発段階です。
開発段階、生産準備段階において不適合の発生を予想し、未然防止をはかる取り組みが源流管理です。
未然防止のための改善では、情報の整理、予想、設計の取り組みが多くなり、そこでは数値データだけでなく、言語情報データの扱いが多くなります。
これら言語情報データの整理や組立などに適した手法が新QC7つ道具です。
この手法によって、物事を論理的に整理し、分析、設計できるようになります。
製造の品質管理の動画も公開中!ご覧ください。
Copyright © 改善と人材育成のコンサルソーシング株式会社