Blog
9.242018
FMEAとは~工程品質を高める5ステップとツール・事例
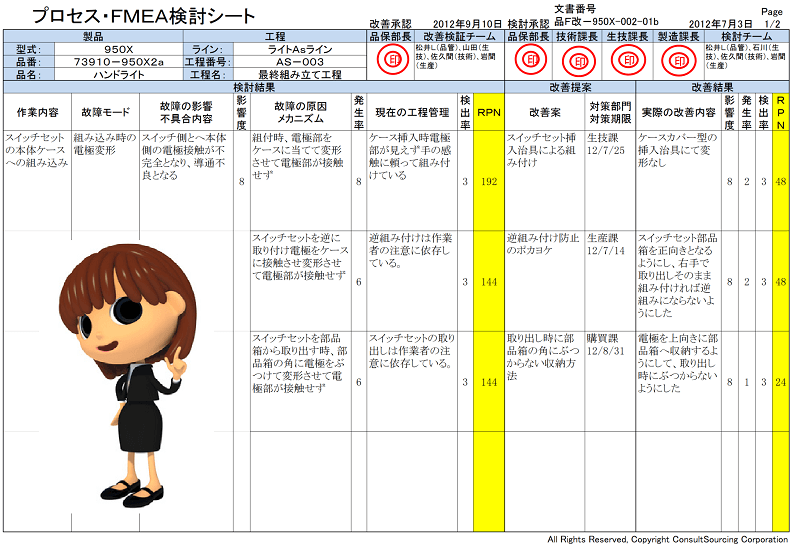
工程FMEAの必要性と実践手順を事例で解説
工程FMEA(PFMEA)とは、FMEA(故障モード影響解析)を工程管理に適用し、製造プロセスの不具合を想定して、未然防止をはかり、工程管理の信頼性品質を高めるための手法です。
このFMEAに変化点管理の考え方を取り入れた手法をトヨタグルーブでは、DRBFMと呼びます。
この変化点管理を付加したDRBFMと同じ工程FMEAの分析と改善の進め方について紹介します。
<目次>
工程FMEAの必要性
工程FMEAとは
・DRBFMとは
工程FMEAの5ステップとやり方
・故障モードの検討のやり方
・影響と発生の分析・改善のやり方
まとめ
工程FMEAの必要性
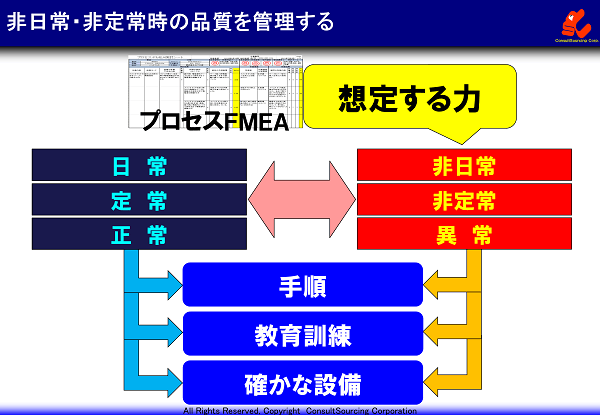
いつもの日常的なこと、あらかじめ規定された定常、作業や設備が正常に運用されていることを前提に、手順の整備や教育訓練、設備の管理をしていませんか?
日常、定常、正常を前提とした管理だけでは、品質管理に抜けがあります。
作業では、いつもと違う、非日常、規定されたこととは違う非定常、正しい条件や使い方とは違う異常な状態が必ず発生します。
この、非日常、非定常、異常状態にあるときも確実に品質を確保できるようにしなければなりません。
しかし、日常や定常、正常だけを前提とした管理では、このような状態の品質を管理することはできません。
そして、非日常、非定常、異常の時が最も品質トラブルが発生しやすいのです。
日常や定常、正常なときよりも品質管理の重要性、優先度が高いのです。
信頼性ある品質管理は、非日常、非定常、異常を想定して、手順の整備、教育訓練、設備管理を行わなければなりません。
非日常、非定常、異常の中で起きる様々な出来事を想定する力を持ち、手順や教育訓練、設備管理に反映する取り組みが必要です。
そして、この様々な出来事を想定するのに、有効な手法が工程FMEAです。
工程FMEAとは
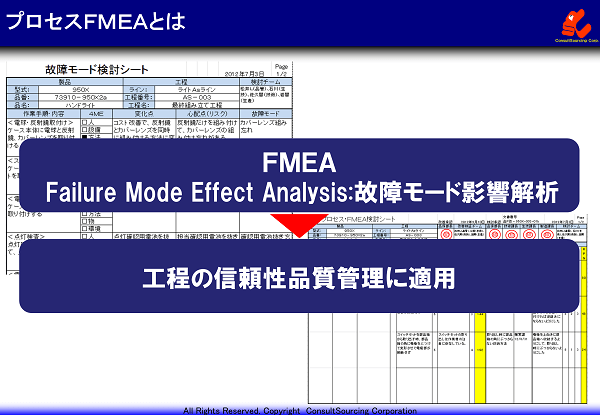
工程FMEAとは、FMEAを工程管理に当てはめたものです。
PFMEA(ProcessFMEAの略)と呼ばれることもあります。
FMEAとは、故障モード影響解析の英語Failure Mode and Effect Analysisの略称です。
製品や製造プロセスの故障やトラブルを想定して、未然防止をはかり、製品や工程の信頼性品質を高めるために考え出された手法です。
製品や製造プロセスの故障モード毎に、その影響、発生頻度、検出の可能性を評価・分析してリスクを評価します。
そのリスクの高さに応じて、対策を行います。
DRBFMとは
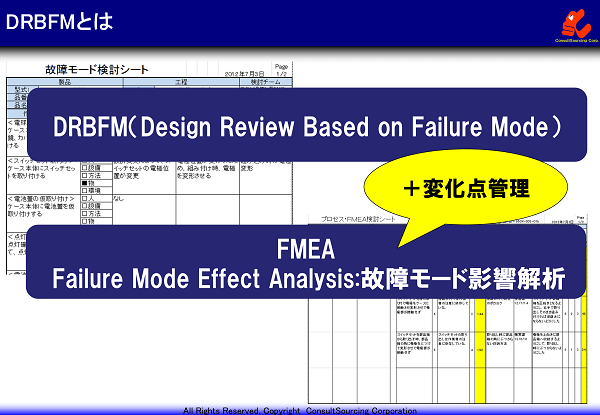
このFMEAに、変化点管理の考え方を取り入れた手法を、トヨタグルーブでは、DRBFM(Design Review Based on Failure Mode)と呼び、運用し製品や工程の故障や不具合の未然防止手法として使われています。
ここでは、変化点管理を付加したDRBFMと同じ工程FMEAの分析と改善の進め方について紹介します。
工程FMEAの5ステップとやり方
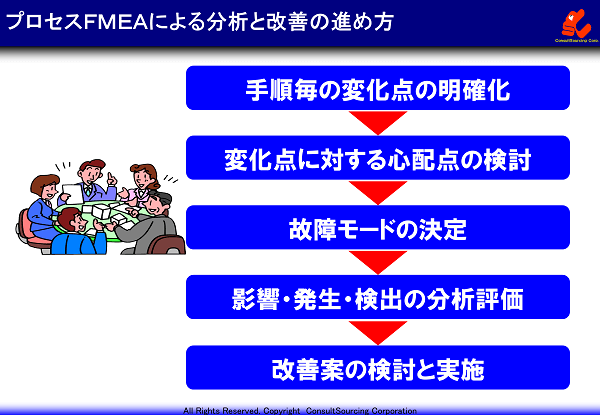
工程FMEAによる工程の不具合などの分析と改善は、営業、製品技術、生産技術、製造、検査、物流など様々な部門の代表者からなるチームによって、専門的かつ多面的な検討を行うようにします。
不具合の起点は、顧客からの要求であったり、技術的背景であったり、設備トラブル、作業者ミスなど、様々なケースが考えられます。
一部の部門だけで行うことは、偏りや抜けのある分析となってしまいます。
できる限り、社内の様々な部門の代表者を集めたチームを編成しましょう。
分析と改善のステップとやり方は、
最初に分析対象の工程の手順毎の変化点を明確にします。
手順の中に潜む様々な不具合を見つけ出すために、変化点に着目する方法です。
次に、変化点に対する心配な点を検討します。
変化は、非日常や非定常な状態を引き起こします。
その変化によって、日常や定常を前提とした作業や設備では対応できない事態を想定します。
心配な点を故障モードとしてまとめます。
工程FMEAでは、工程で起きる様々な不具合を故障モードとして類型化します。
故障モードをもとに、その影響や発生確率、検出の程度を分析し、リスクを評価します。
リスクの程度に応じて、改善の必要性判定して、高いリスクの故障モードは、改善案を立案して改善します。
故障モードの検討のやり方
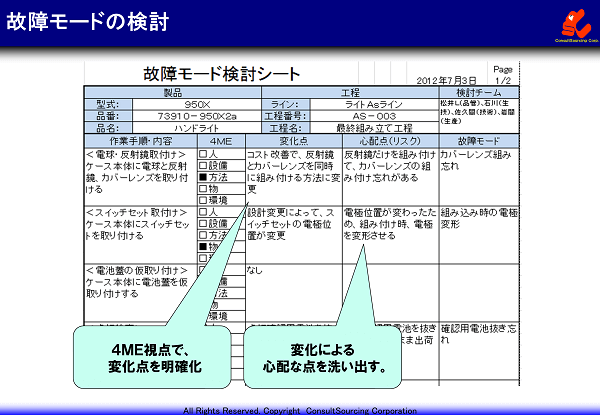
それでは、変化点の明確から故障モードの決定までの具体的な手順について説明します。
故障モードの決定までは、故障モード検討シートを使います。
手順毎の変化点の明確化
まず、作業の手順と内容を書き出します。
1つの機能や部品が作り込まれる単位を1つの手順とします。
作業手順を特定して、検討対象を区分することで、分析範囲を絞り込むことができ、分析精度が高まります。
次に、手順毎の変化点を明確にします。
変化は、人、設備、方法、物、環境の4MEの視点で、今までと変えること、変わることを明確にします。
4MEの視点で整理することで、抜けや偏りを防止できます。
工程の不具合のほとんどは、非日常、非定常、異常な状態のときに発生します。
変化点に着目して、分析することで、的を射た効率的な分析と改善を行うことかできます。
変化点に対する心配点の検討
変化点が明確になったら、その変化によって、引き起こされる可能性のある不具合現象を検討します。
営業、製品技術、生産技術、製造、検査、物流など様々な立場の人の視点で検討することで、多面的、包括的な洗い出しを行います。
今までと何が違うのか、その違いによって、人が間違えたり、重複や抜け、過剰や過小などが発生しないか、イメージして考えます。
故障モードの決定
心配な点が洗い出されたら、それを故障モードとして、まとめます。
変化によって発生するかもしれない心配な点を類型化して、単純化し、まとめます。
心配な点が、製品やサービスにおいて、どのような事象としなって現れるかを一言でまとめます。
背景や条件などを外して、単純な出来事としてまとめるのです。
背景や条件が付いたままでは、影響や原因の分析に、予断を持たせることになり、分析を偏らせたり、客観性を失わせたりすることになります。
故障モードが明確になったら、影響や原因の分析評価を行います。
影響と発生の分析・改善のやり方
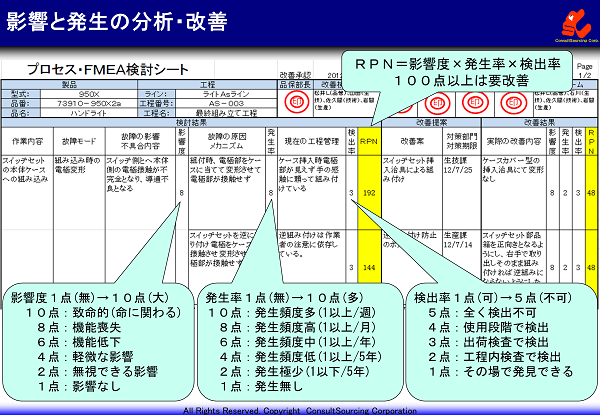
影響や発生分析から改善までは、工程FMEA検討シートを使います。
故障モード検討シートで明確にした故障モードを、作業内容と合わせて書き出します。
すべての作業手順と内容を書き出す必要はありません。
故障モードのある作業だけを書き出します。
影響の分析・評価
故障モードの現象が発生したときの製品やサービスへの影響、不具合内容を検討します。
論理的に、どのように影響があるか明確にします。
影響の大きさを10段階で評価します。
10点が一番影響が大きく、致命的なものです。命に関わる問題といえるものです。
8点は、製品やサービスの基本的機能を失ってしまうほどの影響です。もはや製品・サービスとしの価値がまったくない状態です。
10点と8点の間にあると思われるものは、9点とします。
以下、評価一覧をご覧ください。
評価基準は、企業の信頼性に関する方針、顧客からの期待、製品やサービスの特質などによって異なります。
自社に合った評価基準を設けるようにします。
発生の分析・評価
次に故障モードの発生原因を検討します。
なぜなぜ分析によって、根本原因を探求します。
論理的に説明がつく原因を明確にしなければなりません。
発生率を10段階で評価します。
10点が一番発生頻度が非常に多いものです。週、一回以上の発生する可能性が有り、日常的に起きると考えられるものです。
8点は、月一回以上、起きると考えられる頻度の高いものです。
10点と8点の間にあると思われるものは、9点とします。
以下、評価一覧をご覧ください。
同様に、評価基準は、自社に合ったものにします。
検出の分析・評価
次に、現在の工程管理では、その不具合に対して、どのような管理ができているのか明確にします。
発生を抑える管理や流出を防止する管理の有無や、その程度について明確にします。
現在の工程管理における、その不具合の検出率を5段階で評価します。
現在の管理で不具合を検知できる可能性の度合いです。
5点が一番検出できないものです。まったく検出できません。不具合が製品やサービスに悪影響を起こしてから、初めてわかるものです。
劣化や安全余裕に関するものは、事故が起きるまで、まったく気がつかないものです。
以下、評価一覧をご覧ください。
同様に、評価基準は、自社に合ったものにします。
RPNの評価
そして、影響度と発生率、検出率をすべて掛け合わせて、RPN(リスク・プライオリティ・ナンバー)を算出します。
RPNは、不具合のリスクに対する改善優先度の評価点です。
100点以上は、改善を必要とし、評価点の高いものほど、改善優先度の高いものとなります。
RPNの計算方法、改善判断基準や優先度基準については、自社に合ったものにします。
改善案の検討と実施
改善優先度の高いものについては、改善案を立案します。
原因に対する改善とします。
対策部門、期限も明確にし、改善を提案、勧告します。
改善したものは、あらためて改善後の影響度、発生率、検出率を評価し、RPNを算出します。
RPNが100以上のものは、引き続き改善を繰り返していきます。
まとめ
FMEAとは、故障モード影響解析の英語Failure Mode and Effect Analysisの略称で製品や製造プロセスの故障やトラブルを想定して、未然防止をはかり、製品や工程の信頼性品質を高めるために考え出された手法です。
工程FMEAは、製造プロセスの信頼性品質を高めるための品質保証の一環として行うものです。
信頼性ある品質管理は、非日常、非定常、異常を想定して、手順の整備、教育訓練、設備管理を行わなければなりません。そのために工程FMEAを使ってそれらリスクを想定します。
トヨタグルーブでは、FMEAに変化点管理の考え方を取り入れた手法のDRBFM(Design Review Based on Failure Mode)を使っています。
工程FMEAの5ステップは、変化点の明確化、変化点に対する心配点の洗い出し、故障モードの決定、影響・発生・検出の分析、改善案の検討・実施です。
進め方や評価基準や計算方法などは、信頼性方針、製品・サービスの特性などを踏まえて、自社にあったものをつくり、実践しましょう。
工程FMEAによる分析と改善の進め方の動画を公開中!
Copyright © 改善と人材育成のコンサルソーシング株式会社