Blog
7.92018
QCDSとは~工場管理の品質・コスト・納期・安全の見える化と管理方法
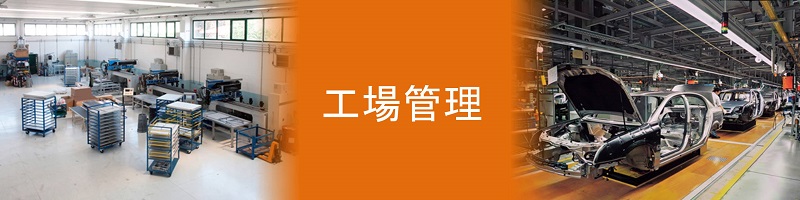
QCDSの見える化によって異常を検知し予防型管理の日常管理力を手に入れる。
QCDSとは、製品や生産活動の評価をするモノサシです。製品や生産活動のQCDSを見える化して不良品・原価高・納期遅延・労働災害の発生防止をすることが工場管理の基本です。QCDSの状態を見える化して異常を検知し予防型の日常管理を実践するための方法とポイントを解説します。
<目次>
QCDSとは
Q:品質の見える化と日常管理のポイント
C:コストの見える化と日常管理のポイント
D:納期の見える化と日常管理のポイント
S:安全の見える化と日常管理のポイント
QCDSとは
QCDSとは、製品や生産活動の評価をするモノサシです。品質(Quality)、コスト(Cost)、納期(Delivery)、安全(Safety)の英語の頭文字からQCDSと呼びます。
製品や生産活動のQCDSを見える化して不良品・原価高・納期遅延・労働災害の発生防止をすることが工場管理の基本です。
Q:品質の見える化と日常管理のポイント
品質を適切に管理するためには、4M(人、設備、方法、製品・原材料)の以下の品質状態を見える化し管理します。
品質における人の管理では、スキル充足率で見える化し、スキルマップを用いて、正しい作業をできる人を沢山つくります。
品質における設備の管理では、工程能力指数で見える化し、管理図を用いて、設備が規定の品質をつくる能力を高めます。
品質における方法の管理では、手順整備率を見える化し、手順整備マップを用いて、組織として正しい作業を定義します。
品質における製品・原材料の管理では、検査合格率を見える化し、品質月報を用いて、製品・原材料が品質規格を満たすようにします。
それぞれについて以下、詳しく説明いたします。
品質における人の管理
良い品質は、正しく作業ができる人から生まれます。
スキル充足率によって各職場における必要なスキルを身につけた作業者がどれほどいるかわかります。
スキルマップは、職場における各作業者のスキル充足率の状態を見える化するものです。
指導できるレベルであれば◎、一人でできるレベルであれば○、援助があればできるレベルであれば△、できないのであれば×として、作業者を評価します。
スキル・マップは、多能工訓練計画表とも呼ばれ、スキルの未熟な作業者の育成計画を立案し、組織のスキル力を高めます。
品質における設備の管理
良い品質は、規定の品質をつくる能力のある設備から生まれます。
工程能力指数は、ある工程の持つ工程能力を、定められた規格限度内で,製品を生産できるか、その評価を行う指標です。
管理された工程は、特性値が正規分布しているので、6シグマで割ったバラツキが両側規格か片側規格の内に収まります。
これを維持するためのツールとして、管理図があります。
管理図は、中心線から管理限界線を引き、その値を超えたものを異常と判断します。
異常の兆候が見受けられた場合は、全数検査などのサンプリング頻度を高めて、異常発生の有無を確認し、異常があれば、ただちに生産を止めて、処置を行いま
品質における方法の管理
良い品質は、正しい作業が定義されていることから生まれます。
手順整備率は、製品ごと、ラインごとなどに作業手順書が、正しく維持されているか教えてくれます。
作業手順書の整備を推進するツールが、手順整備マップです。
手順書が、改訂され合っているのであれば◎、有るが古いのであれば○、作成中であれば△、無いのであれば×とし、各職場の作成状況を、見えるようにします。
組織の手順整備状況が見えることで、リーダーに対し、他職場との優劣を意識させ、自職場の手順整備の動機づけをはかります。
品質における製品・原材料の管理
良い品質は、製品・原材料が品質規格を満たしているものから生まれます。
検査合格率は、ラインや購買先ごとに品質規格に対する合格率を見える化したものです。
どこのラインや購買先が良いか・悪いか、時系列で良くなる方向か、悪くなる方向か、などが見えてきます。
これを管理するツールは、品質月報です。
合格率で順位をつけて、低い順位のライン・購買先社には、品質改善計画の提出、実施状況の報告、監査などを行います。
また、特性項目別に不良率を算出し、高いものには、情報提供と注意喚起を行います。
C:コストの見える化と日常管理のポイント
コストを適切に管理するためには、4Mの以下のコスト状態を見える化し管理します。
コストにおける人の管理では、労働生産性を見える化し、配置図を用いて、生産性が維持された配置にします。
コストにおける設備の管理では、設備生産性を見える化し、設備投入計画表を用いて、生産性が維持された設備稼働にします。
コストにおける方法の管理では、手順別コストを見える化し、ABCを用いて、生産性が維持された手順で作業させます。
コストにおける製品・原材料の管理では、在庫回転率を見える化し、在庫回転率推移表を用いて、滞留・停滞がなく在庫を回転させます。
それぞれについて以下、詳しく説明いたします
コストにおける人の管理
適切なコストは、生産性が維持された配置から生まれます。
労働生産性は、どれだけの人や人件費をかけて、どれだけの生産高や売上をあげるかを示したものです。
より少ない工数で、より高い生産高をあげれば、労働生産性は高くなります。
これらを見える化するツールとして、労働生産配置図があります。
職場ごとの労働生産性の違いが見える化されます。
労働生産性配置図で他職場との優劣を意識させ、労働生産性の劣る職場のリーダーには、どこが問題なのか考えさせます。
コストにおける設備の管理
適切なコストは、生産性が維持された設備稼働から生まれます。
設備生産性は、どれだけの設備投資をかけて、どれだけの生産高や売上をあげるかを示したものです。
より少ない設備投資で、より高い生産高をあげれば、設備生産性は高くなります。
これらを見える化するツールとして、設備投入計画表があります。
設備ごとの製品別の必要数と能力のバランスを見えるようにしたものです。
これにより設備の生産性と必要量に応じた投入計画で、投資対象が明確になります。
コストにおける方法の管理
適切なコストは、生産性が維持された手順で作業することから、生まれます。
手順別コストは、手順を1から書き出し、その手順に対する工数と副材・経費を積み上げたものです。
これらを見える化するツールとして、ABC(活動原価基準管理)があります。
一般的な製造間接費の配賦方法では、大量生産の原価が高く、少量生産の原価が安く見積られることになり、問題がありましたが、ABCでは、製造間接費をコストプールと呼ばれる活動に割り当て、コストプールに集計された原価を製品に割り当てることで適正な配賦が可能となります。
コストにおける製品・原材料の管理
適切なコストは、滞留・停滞がなく、在庫が回転していることから生まれます。
在庫回転率は、どれだけの在庫投入をかけて、どれだけの生産高や売上をあげるかを示したものです。
より少ない在庫投入で、より高い生産高をあげれば、在庫回転率は高くなります。
例えば、在庫回転率が3であれば、1年間に3回転することを表します。
投入した在庫が4か月で売上になっていることを意味します。
在庫回転率は、高ければ高いほどよく、在庫投入されたキャッシュがすぐに売上として回収されるということになります。
これらを見える化する指標として、在庫回転率推移表があります。
製品別の在庫回転率の時間的推移を見える化したものです。
在庫回転の悪い製品には、期首在庫削減の手立てとして購入ロット・頻度の見直し、期末在庫削減の手立てとして長期滞留品の廃棄などで、分母の在庫高を削減するようにします。
D:納期の見える化と日常管理のポイント
納期を適切に管理するためには、4Mの以下の納期状態を見える化し管理します。
納期における人の管理では、非正味作業比率を見える化し、手待ちカウンターを用いて、手待ちがなく正味作業のみで行うようにします。
納期における設備の管理では、正味生産時間比率を見える化し、可動率を用いて、動かしたい時にいつでも動かせるようにします。
納期における方法の管理では、原単位比較表で原単位差を見える化し、詰め替え・積直しがなくモノが流れるようにします。
納期における製品・原材料の管理では、サイクルタイムの差を見える化し、ボトルネックを改善して、工程間の仕掛がなく次工程に流れるようにします
それぞれについて以下、詳しく説明いたします
納期における人の管理
適切な納期・リードタイムは、手待ちが無く、正味作業のみで行っていることから、生まれます。
非正味作業比率は、作業の中に占める付加価値のない非正味作業の割合を示したものです。
一連の作業の中には、運搬、積直し、不良手直し、手待ちなどの非正味作業と加工などの正味作業とその付帯作業があり、この割合が正味・非正味比率です。
通常、正味作業より非正味作業の割合が高いので、改善を行って同じ1割の成果が出た場合、非正味の改善を行った方が、効果は高くなります。
これらを見える化するツールとして、手待ちカウンターがあります。
非正味作業の中でも手待ちは一番のムダですが、また他の作業に埋もれて見えなくなることが多いこともあります。
そこで、手待ちが起こるたびにカウンターを押して、手待ち時間を計測し、見つかった手待ち時間には、別の作業をいれたり、多台持ちや多工程持ちをしたりしながら、手待ちのムダを排除します。
納期における設備の管理
適切な納期・リードタイムは、動かしたい時にいつでも動かせることから、生まれます。
設備には、始業が8時でも8時半にしか良品が出てこない立ち上がりロス、故障により停止する故障ロス、製品切り替え時に発生する段取り・調整ロスがあります。
また、つかみ損ないや落下・転倒などのチョコ停ロス、機械スピードが遅くなる速度低下ロス、不良による不良・手直しロスもあります。
これらのロスは、6大ロスと呼ばれ、これらの積み重ねで、納期遅れの発生やリードタイムの延長が発生します。
正味生産時間比率は、このようなロスと付加価値のある生産時間を積み上げ、正味と非正味の生産時間の割合を示したものです。
このような状態は、可動率でも見ることができます。
可動率は、設備を動かしたい時に、いつでも動いてくれる状態をつくることです。
動作可能時間を、動作可能時間と不可能時間の和で割れば、可動率が導き出されます。
可動率を悪化させるのは、動作不可能時間ですので、この要因をPQ分析などで洗い出し、大きなロスから順番に削減していきます。
納期における方法の管理
適切な納期・リードタイムは、詰め替えや積直しがなくモノが流れることにより、生まれます。
付帯作業比率は、加工時間の正味作業と収容箱入替作業などの付帯作業、運搬、不良品手直し、手待ちなどのムダの割合を見える化したものです。
工程間では、収容箱の員数が異なることにより、詰め替えや積直しが発生します。
その際、用いるのが原単位対比表です。
前工程からの入荷数(入荷原単位)と作業原単位の差を比較する表です。
この差が入荷と作業の原単位の差が大きいと出荷サイクルに対して入荷サイクルが長くなり、注文数が変動した時に入荷待ちの問題を引き起こします。
また、入荷数と作業数が整数倍の関係にない場合、端数待ちなどによって作業が停滞することがあります。
納期における製品・原材料の管理
適切な納期・リードタイムは、工程間の仕掛が無く、次工程にスムーズ流れることにより生まれます。
各工程のサイクルタイムの差を見ることで、どこがどのくらいボトルネックになっているかわかります。
例えば、工程1では、1個120秒で加工が終わります。
工程2には150秒です。工程3は、130秒です。
工程1と2の時間差は30秒ですから、工程1が5個つくる毎に工程1と2の間に在庫が1ずつ積みあがっていきます。
工程2と3の時間差は、20秒ですから、工程3では毎回20秒待たされることになります。
時間差から在庫の積み上がりスピード、手待ち時間がわかりますから、応援体制や中間在庫をどのくらい持たせるか考えてスムーズに流す対策を行いましょう。
S:安全の見える化と日常管理のポイント
安全を適切に管理するためには、4Mの以下の安全状態を見える化し管理します。
安全における人の管理では、安全教育実施率を見える化し、KYTを用いて、決められた安全教育を受けさせます。
安全における設備の管理では、不安全箇所対策率を見える化し、安全赤札を用いて、不安全な状況がない所で作業するようにします。
安全における方法の管理では、ヒヤリハット率を見える化し、ヒヤリハットカードを用いて、重大事故・災害に至る前に対処します。
安全における製品・原材料の管理では、危険原材料数を見える化し、有害材料を取り扱う人や機会を少なくします。
それぞれについて以下、詳しく説明いたします
※安全衛生についての詳しい記事はこちらをご覧ください。
安全における人の管理
安全は、決められた安全教育を受けている人から、生まれます。
安全教育実施率は、法定で定められた雇入れ時教育、職長等の教育、独自の安全衛生教育などの安全教育の実施率です。指導者がいない、まとまった人数が揃わない、忙しくて教育などできない、などできない理由はいくつでも言えますが、教育しないことで休業災害などを起こし、労働基準監督署から操業停止命令でもでれば、会社の信用度や経営にヒビが入ります。
安全教育の一つにKYTがあります。
KYTは、危険予知訓練の略で、作業に潜む危険に気づき、不安全状態や不安全行動に至らないように対策する活動です。
危険を意識させることで、不安全な状態が取り除かれ、不安全な行動に至らないように未然防止となります。
安全における設備の管理
安全は、不安全な状況が無いところで作業することから、生まれます。
不安全箇所対策率は、指摘された不安全箇所に対し、各職場がどれほど対策を実施したかを見える化したものです。
職場ごとに優劣を見える化することで、リーダーの安全意識が高まります。
安全箇所の対策が進まない時は、安全赤札を用います。
安全赤札は、不安全な状態の箇所に赤札をつけ、対策が終わるまで、貼っておくやり方です。
赤札には、担当や期限、対策案などを書かせて、指導します。
視覚に訴えることで、やらざるを得ない雰囲気に持っていきます。
安全における方法の管理
安全は、重大事故・災害に至る前に処置することから、生まれます。
ハインリッヒの法則では、1件の大きな重大事故・災害の裏には、29件の軽微な事故・災害があり、更に、その裏には、事故には至らなかったもののヒヤリとした、ハッとした事例が300件ある、というものです。
このヒヤリとした、ハッとした事例がどの職場にどれほどあるか明らかにしたものが、ヒヤリハット率です。
ヒヤリ・ハットは、ヒヤリ・ハット・カードにして、見える化します。
カードには、工程名、いつ、どこで、誰が、何をしようとしたら、どうなった、ということをまず記入します。
それから、それは何故起きたのか要因を分析し、だからこうしたという対策を書きます。
このようにカード化することでヒヤリ・ハットが明らかになり、重大事故や災害に至ることなく、予防処置が施されます。
安全における製品・原材料の管理
安全は、有害材料を取り扱う人や機会が少ないことから、生まれます。
危険材料取り扱い回数は、そのアイテム数や取り扱う人の人数を明らかにしたものです。
この数が少なければ少ないほど、リスクは低くなります。
前の記事⇒生産管理:結果をつくるための管理指標の6つのポイント
次の記事⇒生産管理:工場長・製造幹部に必要な維持管理力とは
生産管理・現場改善についての研修・診断・コンサルティングの個別相談・お問い合わせ![]() ![]() |
トヨタ生産方式の改善に役立つツール・帳票
トヨタ生産方式のムダとり、見える化、平準化など様々な管理や改善に役立つ実践ツールや帳票を多数公開中!
ツール使い方や管理・改善手法も動画で解説しています。公開ページはこちら⇒「クリック」
Copyright © 改善と人材育成のコンサルソーシング株式会社