Blog
1.82017
工場の生産管理力を高めるための結果をつくる管理指標の6つのポイント
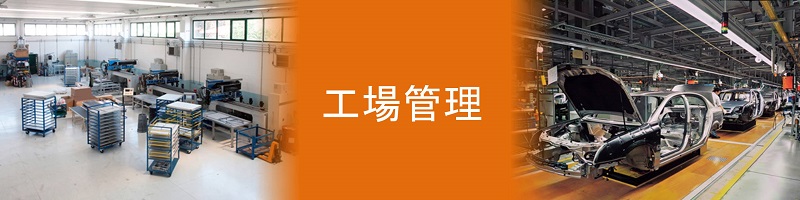
見える化によって変化にチャレンジし結果つくるマネジメント力を高める。
日々の仕事に追われ、目標を達成することを管理するだけが工場の生産管理ではありません。
将来にわたって競争力ある工場とするためには、環境が変わり、生産が変わっても、高い品質と生産性を達成するすることが求められます。そのためには、出た結果を基にした管理ではなく、結果をつくるための管理ができるようにならなければなりません。
見える化によって、めざすモノを部下に見せ、課題を見える化して改善を活性化させ、日常を見える化して日常管理力を高めることが結果をつくるマネジメントです。
結果をつくるマネジメントのための工場まるごと見える化の6つのポイントについて解説します。
<目次>
・結果を基にしたマネジメントの限界
・結果をつくるマネジメントとは?
・結果をつくるマネジメントへ!
・工場のまるごと見える化
・結果指標と管理指標
・管理の2つの領域
結果を基にしたマネジメントの限界
会社や工場の状況を見るためには、財務情報がよく使われます。
財務情報は、損益計算書や製造原価報告書などの形で、期末に明らかになります。
この結果を基に、材料費、労務費、製造経費などを評価し、次期以降の各費用の低減をはかっていきます。
また、製品単位の標準原価計算により、月末に結果として、その差異が明らかになります。
この差異を分析し、改善し、以降の費用低減をはかっていきます。
両者ともに、期末や月末など結果という過去から見るアプローチです。
このようなアプローチでは、前月より材料費が増加しているという数字の結果は、つかめても、その理由が見えません。
例えば、仕様変更があったから歩留りが悪くなったのか、新入社員が増えたから生産性が落ちたのか、装置を修理したはずなのに、何で歩留りが変わらないのかなど、その理由が見えなければ、対策方法がわかりません。
細かい結果情報だけを収集しても、その真因がつかめず、有効な改善指示が出せません。
結果をつくるマネジメントとは?
財務情報や原価計算など、結果を基にしたマネジメントでは、計画と結果に主眼が、置かれます。
そこには、結果に至る途中段階がブラックボックスになってしまい、ストック思考と言えます。
逆に、結果を造るマネジメントは、結果に至る途中の業務活動に主眼を置きます。
計画実現のために、監視を行い、今この瞬間の事実を捉え、改善を行い、その有効性を判断しながら、結果をつくり込んでいきます。
つまり、日常活動の流れに着目したフロー思考と言えます。
結果をつくるマネジメントへ!
結果からわかることは、期末や月末に、単位あたりの生産時間が増して、生産性が劣ってしまい、予実差異が出たということです。
そこに至った過程は、推測でしかものが言えません。
大幅な仕様変更があったのか、新人が配属されたのか、部品の不良が多かったのか、などなぜ予実差異が発生したのかは、わかりません。
本当の原因は何か、何を改善すれば差異が解決するのか、何が最大の問題なのか、をつかまない限り、予実差異を埋めることができません。
工場管理では、大切なのは、このような結果をつくるマネジメントです。
工場を見える化することで、結果をつくるマネジメントが可能となります。
ここでは、結果をつくるマネジメントとしての見える化をご紹介します。
工場のまるごと見える化
工場の見える化は、全社、各部門、個人別に、目標と重点課題、仕事の実施状況、バラツキ、遅れ進み、問題点や、異常の発生状況、処置・対策、行動状況などを経営者や管理者、担当者が、目で見てわかり、改善の展開推進及び日常運営管理において、QCDが低下する前に、事実を的確に把握して、解決のポイントを指摘することができ、その場でアクションをとる予防的管理を実践するやり方です。
今起きている事・今やるべき事など、今この瞬間の状況が一目でわかるようにし、アクションにつなげます。
工場の日々の見える化(オンタイム監視)
月次の結果は、日々の活動の集計です。
日々の活動の中に、仕様変更があった、新人が配属された、設備不良を起こしたなどの生産性阻害要因が含まれていたから、結果として月次の生産性が悪化したのです。オンタイム監視で、今この瞬間現場で起きている事実を見える化しなければ、月末の良い結果にはつながりません。
業務は、常にいろいろな事象によって変化しています。
月次などの平均値では、実際に現場で起きている事象を把握することは困難です。
いろいろな事象が相殺された結果、偶然にも平均値が、予定値と一致した場合には、異常なしと判断されてしまう可能性さえあります。
工場の日々の見える化によって、日次あるいはロット単位などで、行動を監視すれば、現場で起きていることを捕捉することが出来、原因を究明することが、容易になります。
結果をつくるマネジメントは、工場の見える化により行われ、このような日々の見える化と改善の見える化が、欠かせません。
工場の改善の見える化
結果から推測して、あれが問題だろう、だからこうしようと再発防止を考えても、有効な対策につながりません。
日々の事実を判断し、その場で改善すれば、打った手が、良かったのか、悪かったのか、その場ですぐに見えます。
改善策が良ければ、更に、それを深め、逆に、悪ければ、また異なる対策を実行して、生産時間が悪化することを食い止めます。
工場一気通貫の見える化
工場内の各職場のベクトルが異なった方向を向いていると工場に推進力が生まれません。
会社のビジョンからトップダウンで落とした方針・戦略と工場の方針・戦略をボトムアップで融合させ、ベクトルを合わせます。
そうすれば工場内の各職場のめざす姿も同じ方向を向き、相互のシナジーも生まれてきます。
工場の方針・戦略は、トップダウンで、ビジョンから経営戦略、戦略目標、重要成功要因、業績評価指標、ターゲット設定、アクション・プランとなっておりてきます。
現場では、工場管理ボードを用いて、結果指標の設定、目標設定、行動体系、管理指標、行動計画から、活動、指標測定、改善というPDCAを回します。
各現場でのこのようなボトムアップ活動を通じて、目的を確実に達成する管理文化を定着させます。
工場管理ボード
工場の見える化は、各職場に管理ボードを掲げて行います。
工場管理ボードは、各職場(チーム)にて、目的・方針・目標に対する活動状況が、見て分かるようにします。
その目的は、
①必要な情報の形式知化と共有です。
・組織の方針・目的・目標等の形式知化と関係者への周知をします。
・方針、目的を実現するための体制・手段・スケジュールなどを明確にします。
②つながりを明確にします。
・組織の目標と個人の役割・行動のつながりを明確にします。
・目標を実現するために必要な行動を明確にします。
③自律管理をさせます。
・自分たちの進むべき道の認識を高めます。
・適切な活動の継続を自ら監視し、確証を得ます。
・影響が出る前に異常を検知し、アクション(予防・改善)を取らせます。
④組織能力を高めます。
・異能が集い、知識と経験を共有して、新たな気づきを得ます。
・互いに助け合い、励ましあって、組織のストレス耐性を高めます。
・競い合い、刺激しあって、競争心と向上心を高めます。
⑤プライドと責任感を持たせます。
・自分たちの活動を公共の場に示し、活動に対するプライドと責任意識を高めます。
⑥現地・現物・現認の三現主義で推進します。
・経営者、幹部が現地・現物・現認で、管理・改善活動にコミットする場をつくります。
プロセス管理と見える化
工場の方針・戦略は、目標管理におとされます。
目標として、生産高、利益、品質、原価、納期、在庫、調達、人員などの計画や予算が立てられます。
その計画・予算に対し、予実進捗、ライン別損益計算、機械別損益計算などのプロセス管理をすることで、結果としての実績管理につながります。
このプロセス管理を現場で行うことが、目で見る管理です。
プランでは、目的・優位性・成長目標・制約・環境などのめざす姿を見える化して、ドゥーでは、結果と行動の連鎖、管理指標など行動を見える化して、チェックでは、バラツキ異常、行動異常、結果異常など異常を見える化して、アクションでは、原因、改善案、標準化など改善を見える化して、部下に管理の目的・狙いを周知します。
結果指標と管理指標
現場では、管理活動を適切かつ合理的に行うために、管理の対象として管理項目を取り上げます。
取り上げた項目は、管理特性と言われ、その管理項目に対する尺度(ものさし)です。
管理項目には、結果系の管理項目と要因系の管理項目があります。
結果系の管理項目は、最終的に会社が求める数字でありますが、現場の管理は要因系の管理項目が必要となります。
結果系の管理項目としては、結果指標があります。
結果指標は、計画や予算に対する結果であり、仕事の実施成果を表します。
生産高1億円などのように結果系の定量的な目標を設定します。
要因系の管理項目としては、管理指標があります。
管理指標は、結果に至るプロセスを管理し、仕事の異常の有無や程度を明らかにするものです。
結果指標の生産高1億円を達成するためには、設備可動率向上などのように結果に導くためのプロセス管理項目を指します。
管理指標の項目を管理することで、結果指標につながっていきます。
結果指標の例
結果指標の例としては、経常利益を高める指標があります。
ボリュームとして、売上高、受注高、生産高、在庫高など、原価として、販管費、製造原価、仕入原価、更に、品質や納期などがあります。
売上高からは、各項目を更に、製品別、顧客別、ライン別、材料別、などに細分化していきます。
原価も同様に、販売費、管理間接費、人件費、製造経費、原材料、外注加工費などの項目に細分化します。
プロセスと結果指標から正しい行動を定義
良い結果指標に導くためには、そのプロセスを管理しなければなりません。
各プロセスの中で、正しい行動を定義します。
例えば、設計プロセスでは、材料取りの効率化、試作廃棄最小化、仕入れプロセスでは、価格交渉・転注、代替品への転換、加工プロセスでは、外注先の変更、有効期限切れ廃棄レス、組立プロセスでは、ミスによる廃棄レス、再検査の削減などを、正しい行動として定義します。
管理指標で正しい行動がされているか測定
結果指標を達成するために、定義された正しい行動を行います。
その際、正しい行動が適切に行われているか行動を測る指標が必要になります。
これが、管理指標であり、行動指標とも言われます。
管理指標は、作業に負担をかけることなく、測定が可能になるようにします。
例えば、材料取りの効率化に対しては設計使用率、試作廃棄最小化に対しては施策廃棄率、価格交渉・転注、外注先の変更に対しては市場最安値差異、代替品への転換に対しては代替品転換率、有効期限切れ廃棄レスに対しては期限切れ廃棄率、ミスによる廃棄レスに対してはミス廃棄率、再検査の削減に対しては単位あたり検査回数などを管理指標に定めます。
管理指標を使って正しい行動のPDCAを管理
例えば、管理指標をミス廃棄率とし、5%以下に設定します。
毎日その指標を測定し、グラフなどで見える化します。
その限界ラインを超えたところが、異常です。
このまま放置すれば、ミスによる廃棄レスという正しい行動が維持されなくなります。
異常が、目で見る管理をされることにより、その異常を正常に戻そうとするPDCAができます。
管理の2つの領域
管理とは、目的を継続的に効率よく達成するための一連の活動です。
計画(Plan/Standard)-実行(Do)-評価・確認(Check)-処置(Act.)を回していくことで、問題を解決します。
管理には、維持の管理と改善の管理があります。
維持の管理は、スタンダードとして決められた正しい手順・やり方・方法・標準などを、維持することです。
そのためにPDCAのサイクルを回しながら、日常管理として、現状を維持することを管理します。
改善の管理は、守ることから、破り、更に一歩先に離れる、守破離を行いながら、より良い手順・やり方・方法に改めていくことです。
PDCAのサイクルを回しながら、改善管理として、現状打破し、成長することを管理します。
日常管理
工場管理の基本要素には、品質機能(Q)、原価機能(C)、量・納期機能(D)、安全機能(S)があります。
工場経営は、これら機能が適切に働くことで、結果が生まれますので、これら機能に着目した管理が必要となります。
工場管理では、基本要素ごとに目標を定め、それを実現するための各部門の役割と連携の適正化と調整を図っていく機能別管理を行います。
改善管理
方策とは、改善目標達成のための手段であり、目標達成を阻む課題や問題の解決をはかるものです。
改善管理の方策には、技術系方策として、技術の調達や開発、人的リソース系の方策として人的リソースの調達や開発・向上、プロセス系方策としてプロセスの調達や開発・向上、更には、撤回や回避などの領域があります。
前の記事⇒生産管理:工場の日常管理力を高めるための4つのポイント
次の記事⇒生産管理:工場長・製造幹部に求められる3つの能力とは
生産管理・現場改善についての研修・診断・コンサルティングの個別相談・お問い合わせ![]() ![]() |
トヨタ生産方式の改善に役立つツール・帳票
トヨタ生産方式のムダとり、見える化、平準化など様々な管理や改善に役立つ実践ツールや帳票を多数公開中!
ツール使い方や管理・改善手法も動画で解説しています。公開ページはこちら⇒「クリック」
Copyright © 改善と人材育成のコンサルソーシング株式会社