Blog
7.172018
トヨタ生産方式の工程管理とは~流れを整えて工程と作業を計画して管理する方法と事例
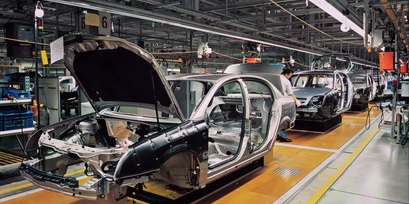
流れを整えて工程と作業を計画して管理する方法。
トヨタ生産方式の工程管理の極意は、流れをつくることです。工程の入口から出口までの流れを停滞させることなく、“細くて速い”流れにします。
どのように生産工程を管理するのか、流れでモノをつくるための管理視点、コスト設計、工程設計、作業設計、原単位表の作成、小ロット生産化と段取り改善のポイント・コツを説明します。
<目次>
1.流れでモノをつくるための管理
2.工程管理では在庫はリードタイム
3.コスト設計のポイント
4.工程設計のポイント
5.作業設計のポイント
6.原単位表の作成ポイント
7.小ロット生産化と段取り改善のポイント
流れでモノをつくるための管理
トヨタ生産方式の工程管理の極意は、流れをつくることです。
工程の入口から出口までの流れを停滞させることなく、“細くて速い”流れにします。
流れとは
モノを仕入れたり、つくったりする場合、大量に仕入れたり、大ロットでつくった方が安くなるという観念があります。
確かにその時点の仕入単価/製造単価は、安く見えます。
しかしながら、その製品が、完成して売れてはじめて現金が回収されます。
初期段階で安く仕入れ/つくっても、それが在庫として残れば、現金は回収されず、キャッシュフローが滞ります。
つまり、在庫を持つことで、資金が在庫に化けてしまい、現金を遊ばせることになります。
大量仕入や大ロット生産は、投入資金も大きくなり、金利負担がかさみ、回収も長期間となります。
このように儲けるための視点を、ある時点で考えるのではなく、期間として捉えて収益性を判断します。
細くて速い流れ、つまり、小さな単位で速くつくり、早く売り、早く現金に変えていくことの方が、収益性は高まります。
その効果は、
①必要なキャッシュフローの減少
②在庫による金利負担の軽減
③オーダ打ち切り時の在庫リスクの軽減
④部品手配、在庫管理などの間接費の低減
⑤在庫スペース減少による多目的転用
など形で現れ、経営体質の強化に繋がります。
細くて速い流れをつくる
流れをつくるとは、在庫をかかえてその在庫から出荷する(ストック思考)のではなく、在庫を持たずに顧客が要求したものをいかに早くつくる(フロー思考)ことです。
団子状態でまとめてつくる太くて短い流れではなく、小さな単位で速くつくり、細くて速い流れで整流化します。
これにより、リードタイムが短縮され、
①売れるものを売れる時にタイミングよく生産できる
②市場の変動に即応できる
③在庫、死蔵品、捨てるムダが少なくなる
④設計変更に即応できる
⑤不良などのフィードバックが早くなり不良対策が迅速になる
⑥生産計画の確定を遅らせることができるため、見込み違いなどの変更が減る
⑦生産計画とその遂行能力が向上する
⑧飛び込み、特急が発生しても迅速に処理できる
⑨異常が分かりやすくなる
⑩つくる能力が強化される
などの効果が生まれます。
工程管理では在庫はリードタイム
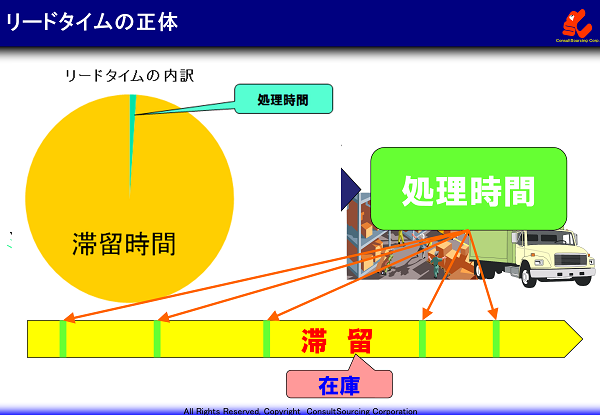
リードタイムが長いということは、その間にある在庫も膨らんでいると言えます。工程間の在庫は、それを“停滞”と見なし、生産プロセスにおける“待ち時間”ととらえます。
トータル・リードタイム
トータル・リードタイムとは、調達リードタイム+生産リードタイム+物流販売リードタイムになります。
中でも、生産リードタイムは、原材料が工場に入り加工され出荷されるまでの時間を指します。
生産のリードタイム
受注を受け出荷されるまでの生産リードタイムは、加工時間+停滞時間で構成されます。
加工時間とは、いわゆる作業時間のことで、付加価値を生む正味作業時間と付加価値を生まない付帯作業時間(作業準備時間)に分けることができます。
停滞時間とは、加工を待っている待ち時間(作業待ち時間)のことで、ロット形成されるための待ち時間、運搬している待ち時間、手待ちとなっている待ち時間、などがあります。
生産のリードタイム=加工時間(正味作業時間+付帯作業時間)+停滞時間(情報の停滞時間+検査時間+運搬時間+手待ち時間+・・・)
加工時間の短縮より停滞時間の短縮
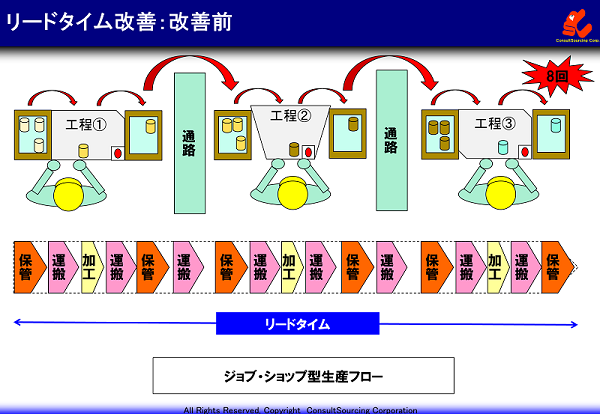
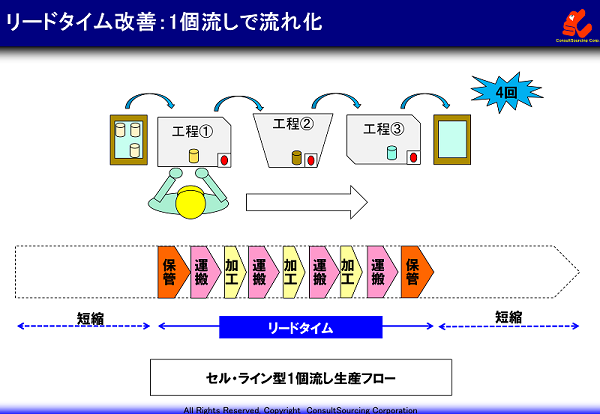
例えば、あるプレス工程における1枚のプレス製品をつくるための生産リードタイムを、加工時間(1ショット10秒)+情報の停滞時間(2日)+検査時間(1分)+運搬時間(1時間)+手待ち時間(20分)と仮定します。
これを比率であらわすと、
加工時間:停滞時間=10秒:86,400秒+60秒+3,600秒+1,200秒=10:91,260=1:9,126となります。
つまり、加工時間1に対して、停滞時間の割合は9,126です。
この意味するところは、改善の狙いどころを、加工時間の10秒を狙うより、同じ10%改善するのであれば、停滞時間の91,260秒を狙った方が、効果が高いということです。。
改善の狙いどころは、まずは停滞時間であり、流れをつくることで大きな効果が生まれて、在庫が削減されます。
リードタイムを短縮すれば品質が向上する
リードタイムが長くなれば、そこかしこに仕掛品や完成品で在庫が膨れ上がり、運搬や保管の際に破損や劣化が生じます。
つまり、リードタイムの短縮は、このような破損や劣化が削減され、品質は向上します。
コスト設計のポイント
販売価格と予定利益から目標とする製造原価を求め、その原価に収まるように工程や設備、作業の調整と改善を行っていきます。原価積み上げて考えるのではなく、目標原価に収まるように様々なことを設計していきます。
目標原価の設定
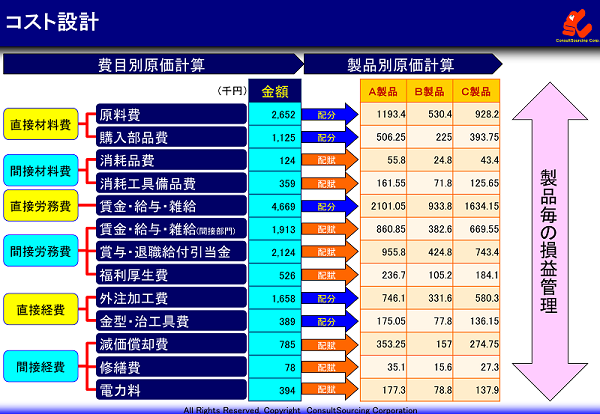
目標とする製造原価を決定します。
原価積み上げ方式ではなく、予定販売価格(工場卸価格)から予定利益を引いた額を目標製造原価とします。
目標製造原価を内外区分や機械化、原材料・部品調達見積を考慮し、原材料費、外注費、副資材費、設備償却、人件費、光熱費などに目標原価を設定して、コスト設計書に記入します。
原価見積もりと差異分析
予想販売量と工程設計結果などからライン稼働条件などを設定して、各費目の原価を見積もります。
見積りでは、試作での工程毎の加工時間、作業時間、不良率なども考慮します。
コスト設計書によって設定した目標原価と見積もりとの差異を整理・分析して改善を行っていきます。
全体を見渡して差異の大小が少なくなるように目標原価の割り付けの見直しをします。
労務費については各工程の内外製の見直し、機械化と手作業区分の見直しなどによって費目間の比較、作業改善などによる作業時間の短縮を検討します。
原材料費や梱包費などは材料取りや歩留まり、梱包方法の見直しによって、原材料・梱包材の使用量の削減、調達先の見直しによる調達価格の削減を検討します。
設備償却費、消耗工具費などは、使用する設備や工具の仕様やメーカーの見直しによる初期投資額の圧縮を検討します。
設備投資額の設定
目標原価から割り付けられた設備償却費から投資可能金額を算出します。
工程設計での必要設備の見積りを考慮し、各工程の設備投資額を設定します。
必要投資額と設定投資額に差がある場合は、機械化と手作業分の見直し、外部委託などを含めて設定投資額に収まるように調整と改善を行います。
人件費と投入人員の決定
目標原価から割り付けられた人件費から投入可能人数と総作業工数を算出します。
工程設計で必要とされる作業時間から必要総作業工数を算出します。
必要総作業工数と割り付けられた総作業工数に差がある場合は、各工程の作業時間の見直し、作業改善、外部委託など含めて割り付けられた総作業工数内に収まるように調整と改善を行います。
工程設計のポイント
工程とその順番、必要設備、加工時間(マシンタイム)と作業時間の設計をします。相反関係にあるコストと品質を両立させるために調整と改善を行い、各工程の処理能力の差が少なくなるように設備などの能力と配置を調整します。
個別工程の設定
規定された製品品質をつくり込むために必要な工程を明確にします。
類似する加工や処理、組み立ては集約して工程数が少なくなるようにします。
工程設計書などにより工程での加工・処理範囲がわかるようにします。
加工・処理上の課題などがある場合はそれを明記し、実現可能性を検証します。
実現可能性が低い工程については代替え工程を検討しておきます。
工程順の設定
安定した品質と最短のリードタイムで製品をつくるための工程順を明確にします。
外部への委託工程についてはまとめて出て行くようにし、出入りの回数が少なくなるようにします。
平準化改善なども含め、工程間に滞留在庫ができないようにスムーズな流れとなるように工程順番を設計します。
内外区分の設定
個別工程の設定を受けて、各工程の内外製の区分をします。
品質面、コスト面、物流面を考慮し、各工程を内製化した場合と外部委託した場合のメリット・デメリットを分析し、購買政策も勘案した上で内外区分を決定します。
機械化と手作業の区分
各工程の機械化とするか手作業とするかの区分をします。
品質面、コスト面、将来の拡張性などを考慮し、各工程を機械化した場合と手作業とした場合のメリット・デメリットを分析し、自社の技術革新の方針も勘案した上で、区分を決定します。
投入設備の設定
各工程に必要となる設備の仕様、台数などを明確にします。
コスト設計で割り付けられた投資額に収まるように、工程で必要とする機能・性能の範囲で検討し、過剰な機能・性能は付加しないようにします。
特にマテハンなどの取り付け・搬送系の機械化は、原則手作業にします。
工程毎の加工時間(マシンタイム)と作業時間の設定
各工程での必要な加工時間(マシンタイム)、作業時間を設定します。
コスト設計で割り付けられた工数内に収まるように調整と改善を行います。
標準作業組合せ票などを使って、加工サイクルタイム(マシンタイム)と作業時間のバランスがとれるように作業時間の割り付け設計をします。
工程毎の作業内容・品質特性・製造条件の設定
各工程の作業内容や機械による処理内容を設定します。
どのような作業を行うのか割り付けられた作業時間や加工時間を考慮して決定します。
工程によってつくり込む品質についてその品質特性を設定し、その品質をつくり込むための製造条件も明らかにします。
品質特性は、設計図で示された寸法公差や機械的特性などをどの工程でつくり込むのかを明らかにして決定していきます。
製造条件は、品質特性と作業時間・加工時間などを考慮し、設備特性や利用できる技術レベルを参考にして決定します。
作業設計のポイント
作業内容と手順を設計します。作業を早く安定してできるように改善するとともにそれを補助する仕掛けツールを準備します。
工程毎の作業内容の設定
規定された製品品質をつくり込むために必要な工程における作業内容を設定します。
品質を確保する上で重要な作業事項を明確にします。
作業手順書などにより工程毎の作業範囲・アウトプットなどがわかるようにします。
作業上の課題などがある場合はそれを明記し、実現可能性を検証します。
実現可能性が低い作業については代替え作業を検討します。
作業手順の設計と改善
設定された作業内容とアウトプットを割り付けられた作業時間内で実施するための作業手順を設定します。
標準作業三票などを使って、目標時間内に収まるように作業改善を繰り返し、手順を設計していきます。
作業改善を通じて得られた作業のカンコツなどは作業手順書など明記し、共有します。
作業の急所の明確化
規定の作業スピードで担当する作業者に作業を実施してもらい、ミスのしやすい箇所などを洗い出し、作業をする上で特に気をつけ無ければならないことを「急所」として明確にして、作業手順書に明記して共有します。
異常処置方法の明確化
工程FMEAなどの分析や、実際の作業経験から、作業にて発生する異常を洗い出し、その異常処置方法を検討して、手順書に明記します。
異常処置では、被害の拡大や二次被害の防止のために「止める・呼ぶ・待つ」を基本原則として、作業者がやって良いことといけないことを明確にわかるように記載します。
品質確認事項の設定
適切な作業が実施されたことを確認するための品質確認事項を明確にして、作業手順書に明記して、確認することを徹底します。品質確認事項は、QC工程表によって規定された項目であり、作業準備、設備や治工具の設定、製品品質が適切であることを現場で確認する項目です。
原単位表の作成ポイント
各工程のコミュニケーションや連携ができていないとそれぞれが自工程のつくりやすい、或いは自工程のみの経済性を考えた勝手なロットサイズや納期でつくってしまう場合があります。
このような時に各工程のつくりの現状を原単位表にまとめます。
原単位表の目的
原単位とは、一つの部品・製品をつくるためにかかる必要工数・設備の正味工数などのことで、原単位表はライン・部品・設備ごとなどに生産数・荷姿・設備負荷・必要工数・負荷率などを一覧表にしたものです。
原価を把握する道具だけでなく、各工程の流れをつくりやすくするために、設備・工程へのものの流し方、変動を最小にする仕掛け、人員配置などの改善の道具としても使われます。
原単位表の作成手順
各工程において、以下のような項目の値を調査し、原単位表にまとめます。
①品名(工程名)、品番
②収容数
③必要数
④タクトタイム
⑤ロットサイズ
⑥段取り替え工数(時間)、回数; 現時点で生産している製品の加工が終った瞬間から次に生産する製品の型などを交換して次の部品の良品1個目ができるまでの時間、回数
⑦正味工数(時間); 主体作業を順序通りに1サイクル行なった時の最小時間(サイクルタイム)
⑧付帯工数(時間); 主体作業の準備に必要な時間
⑨必要工数 ; 正味工数+付帯工数+段取り替え時間
⑩必要人工 ; 定時間内で月間必要数をつくるのに必要な人数(必要人工=必要工数×月間必要数÷月当たり稼働時間)
⑪マシン・サイクルタイム(MCT); マシンタイム(起動スイッチを押してから加工が完了し元位置に戻るまでの時間)+設備にかかる手作業時間
⑫生産時間 ; 1ヶ月で設備が何時間動いているか(稼動時間)
⑬その他 ; 稼動日数/月、稼動時間/日、定時内時間、仕掛けの形態、引きのサイクル、納入サイクル、現状人数、ネックマシンなど
小ロット生産化と段取り改善のポイント
細くて速い流れでモノをつくろうとすると、大ロット生産していた工程では規模の経済性を犠牲にしてでも小ロット生産にし、小刻みにモノを流すことに努めます。
個々の能率は、必ずしも全体の効率に結びつきません。
大ロット生産の弊害
大ロットで生産する理由は、
①段取り替えが下手で時間がかかる
②ロットが大きいと品質が安定する
③設備が高価で、止めると損をする
④調整が多くせっかく良い条件が出せたから出来るだけ連続させたい
などが考えられます。
この結果在庫が増え、保管の場所や容器が必要となり、それを管理する人も増えます。また、不良品が発生した時は、すぐライン停止することができずロット単位で不良が発生してしまい、後からの追跡も困難となってしまいます。本当に必要な設備能力や人が見えなくなり、死蔵品も増加してしまいます。
小ロット化と段取り替えの関係
従来の大ロット生産から、単純に段取り替え回数を増やせば、必要工数(正味工数+付帯工数+段取り替え工数)が増え定時オーバーとなってしまいます。
そこで、小ロットでつくるためには、定時内で収まるように、段取り替え時間の短縮が求められます。
また、定時割れしているラインでは、新たな品目を加えることで定時分の仕事を与えることをしますが、新たな品目が増えればそこには品種切替のための段取り替え作業が発生します。
このように多品種少量生産になっても定時内に収まるような段取り替え時間の短縮は、改善ニーズとなります。
段取り替え時間
段取り替え時間とは、現時点で加工している部品の加工が終わった時から、次に生産する部品の型や刃具などを交換して次の部品の良品1個目ができるまでの時間を言います。
総段取り替え時間=
内段取り替え時間(機械を停止させないとできない段取り替え作業時間)
+調整時間(段取り替え後、品質の精度確保やトラブル処理のため機械が停止する時間)
+外段取り替え時間(機械を停止させずにできる段取り替え作業時間)
段取り替え改善のステップ
段取り替え改善は、以下の順で進めます。
①内段取り作業と外段取り作業を分ける; 内段取り作業・調整作業・外段取り作業を明確に分ける。
②内段取り作業を外段取り作業に移す; 材料の準備、型・治工具・刃具の点検整備・取りそろえ・後片付け、標準類・ゲージの準備と後片付けなどを外段取り作業に移す。
③内段取り作業を短くする; 金型・治工具・刃具をワンタッチ化にする、平行段取り替え作業の実施、段取り作業の標準化、作業訓練、などで内段取り作業を短くする。
④調整時間を短くする ; 調整作業を外段取りに移すなどで調整時間を短くし、調整レス(調整時間ゼロ)を目指す。
⑤外段取り時間を短くする; 準備完了品置き場の指定、外段取りトラブルの改善、使用済み金型・治工具・刃具などの整備と整備手順の標準化を行う。
段取り替えの標準化
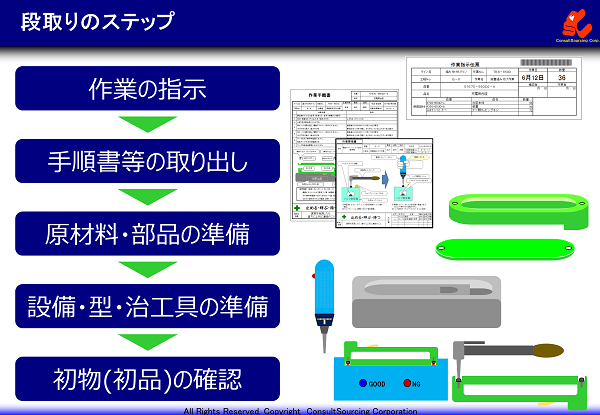
段取り替えは、誰がいつ行っても同じようにできるようにしなければなりません。
そのために手順書をつくり、その手順通りにできるように訓練します。
段取り替え改善の現状把握から歯止めまで、段取り替え改善実施計画書を作成して進めていきます。
前の記事⇒小ロット生産とは~導入の進め方と事例
次の記事⇒かんばん方式とは~導入と進め方・事例
※標準作業・ライン改善の推進責任者・事務局・リーダー必携のガイド提供中!
Copyright © 改善と人材育成のコンサルソーシング株式会社