Blog
5.282016
トヨタ生産方式:整流化改善とは~工程の流れ化の進め方・事例

モノと人と情報の流れを整える工程の流れ化改善の進め方
ムダ取り改善ができ、個々の職場の標準化が図られると、次は個々の前後工程を合わせて連結した1本の工程として整流化を図ります。
整流化=工程の流れ化とは、流れでモノをつくることです。
流れの滞るところにはモノの停滞が生じ在庫が発生します。
流れを良くする狙いはリードタイムの短縮です。在庫が削減されればリードタイムが短くなり、品質も向上します。
工程間の停滞(=在庫)を削減することでトータルリードタイムが削減し、生産性も高めるとができます。
<目次>
整流化(工程の流れ化)のねらい
現在のモノの動き(流れ)を見る
モノの動きを流れ化する
1個流しで流れ化する
生産フローを流れ化する
人の動きのムダを排除し作業を流れ化する
リードタイムとは
リードタイム短縮の進め方
整流化(工程の流れ化)のねらい
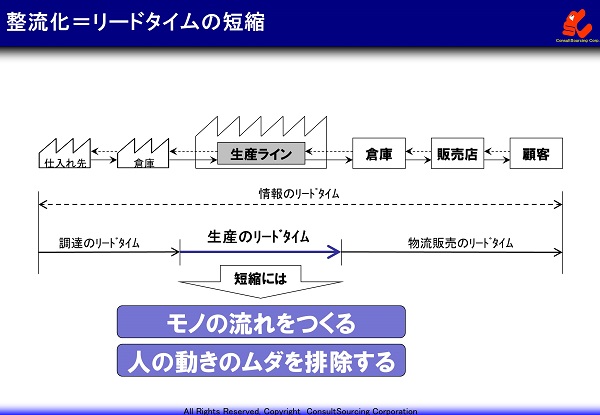
リードタイムには、調達リードタイム・生産リードタイム・物流販売リードタイム・情報リードタイムなどがあります。
整流化とは、トータルリードタイムを短縮することですが、特に生産リードタイムを短縮し、流れでモノをつくることが重要です。
流れの無いところには、停滞が生じ在庫が発生し、リードタイムが長くなります。
それにより、在庫スペースを確保するムダ、積み替え・詰め替えなどの運搬のムダ、パレット・収容箱・リフトなど運搬具のムダ、オーダー打ち切り時の在庫リスクのムダ、品質劣化・陳腐品・長期滞留品・死蔵品などのムダ、電気・エアー・倉庫代など経費のムダ、帳簿と現物の在庫管理のムダなどが生じます。
その結果、在庫や資金が回転せず、キャッシュフローを悪化させてしまいます。
そこで、リードタイム短縮をはかるのが、整流化改善です。
整流化による流れでモノがつくれるようになれば、
① 売れるものを売れる時にタイミングよく生産できる、
② 市場の変動に即応できる、
③ 在庫、死蔵品、捨てるムダが少なくなる、
④ 設計変更に即応できる、
⑤ 不良などのフィードバックが早くなり不良対策が迅速になる、
⑥ 生産計画の確定を遅らせることができるため、見込み違いなどの変更が減る、
⑦ 生産計画とその遂行能力が向上する、
⑧ 飛び込み、特急が発生しても迅速に処理できる、
⑨ 異常が分かりやすくなる、
⑩ つくる能力が強化される、
というようなメリットが生まれてきます。
このような整流化を進める上での、モノの流れのつくり方、人の動きのムダを排除した作業の流れのつくり方を解説いたします。
◆リードタイム短縮で出る抵抗
リードタイム短縮の効果は分っていても、実際行おうとすると以下のような抵抗が現場から出てくる場合があります。
①在庫切れが起こると怖い
②操業度が低下する
③段取り替えを多くすると作業能率が下がる
④まとめ生産した方が早いし、効率がよい
⑤伝票発行などの事務処理が増える
⑥余裕をもってつくった方が安心
最初に、整流化のねらいと効果をしっかりと伝えるようにしましょう。
現在のモノの動き(流れ)を見る
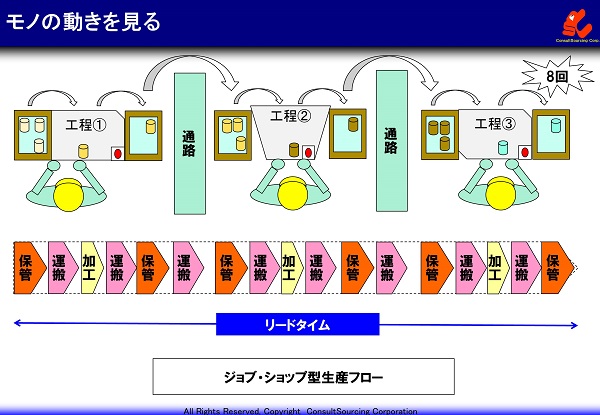
モノの流れをつくるには、まずモノの動きを見ます。
事例では、工程が①から③まで、3つに分かれています。
工程①ではパレット上の収容箱から材料を取り、加工し、収容箱へ納めます。
収容箱が、一杯になれば、入れ替え、次の収容箱に収め、パレット上の収容箱をすべて一杯にします。
パレット上が一杯になれば、パレット単位で工程②に運搬します。
工程②でも同様に、保管、運搬、加工、運搬、保管というプロセスを経て、工程③に運搬されます。
これを工程③まで繰り返すと、加工3回に対し、保管・運搬回数は8回にも及んでおり、リードタイムは長くなっています。
このような生産形態は、一般的にジョブ・ショップ型と言われています。
モノの動きを流れ化する
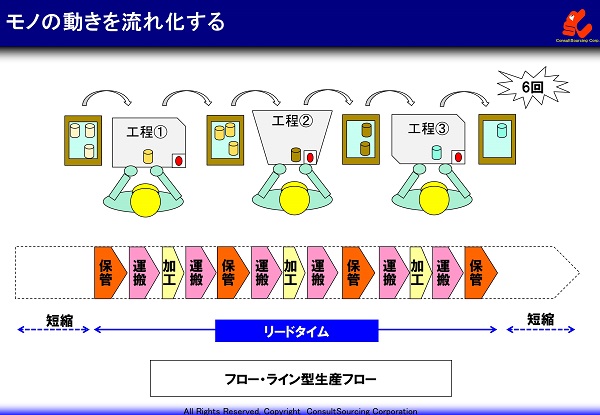
先の事例では、工程ごとにまとめてつくり、まとめて運搬するというスタイルから、保管・運搬が流れを阻害していましたので、この保管・運搬回数を減らすことで、流れをつくります。
ここでは、工程間の通路をなくし、収容箱単位で次工程に送ります。
このようにすることで、保管、運搬回数が削減され、加工3回に対し、保管・運搬回数は6回となり、リードタイムは短縮されます。
このような生産形態は、一般的にフロー・ライン型と言われています。
1個流しで流れ化する
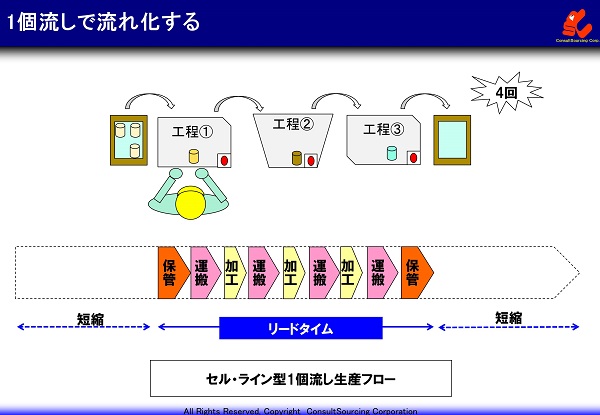
更に、モノの動きを流れ化します。
工程には、設備の能力があります。
早い時間でつくれる工程と時間のかかる工程が存在します。
このような工程の能力差を在庫で補うことで、流れをつくったのが、先ほどのフロー・ライン型でした。
在庫でバッファーを持つ分、保管・運搬回数はまだ残っています。
本例では、工程間の在庫をなくし、1個流しで次工程に送ります。
1個流しにするためには、工程間の能力差を在庫でなく、負荷を平準化し、作業バランスを取らねばなりません。
各工程がそれぞれ同じ時間で作業できるような同期化をはかり、流します。
このようにすることで、保管、運搬回数が極端に削減され、加工3回に対し、保管・運搬回数は4回となり、リードタイムは更に短縮します。
このような生産形態は、一般的にセル・ライン型と言われ、通常、U字型ラインで設計されます。
生産フローを流れ化する
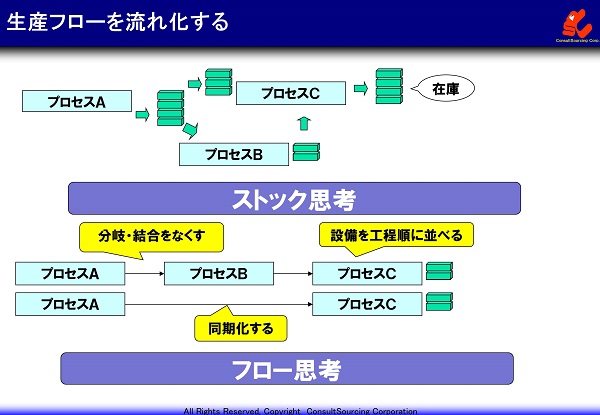
生産フローを流れ化します。
ジョブ・ショップ型は、まとめてつくり、まとめて運ぶストック思考です。
工程間で在庫が生まれ、その都度、保管・運搬が生じます。
フロー・ライン型やセル・ライン型はフロー思考です。
工程の分岐・結合をなくし、設備を工程順に並べ、工程の同期化をはかり、流れをつくります。
人の動きのムダを排除し作業を流れ化する
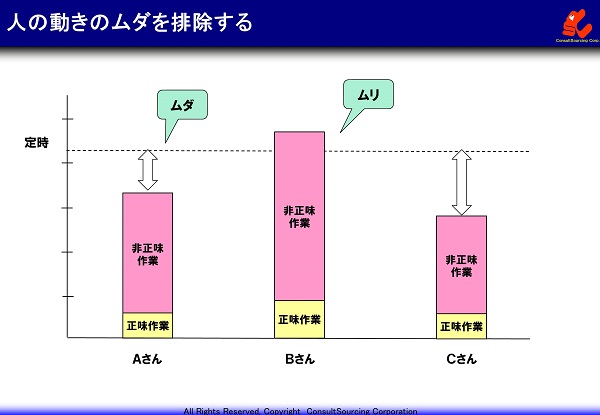
工程を流れ化するとともに、作業も流れ化します。
組立作業ラインに3人の作業者がいます。
AさんとCさんは、定時割れの作業量しかなく、ムダと言えます。
Bさんは、定時に対し作業量がオーバーしており、ムリしていると言えます。
このような作業のバランスが悪いと、作業者間で在庫の発生や手待ちを生み、作業の流れが阻害されます。
非正味作業を見える化する
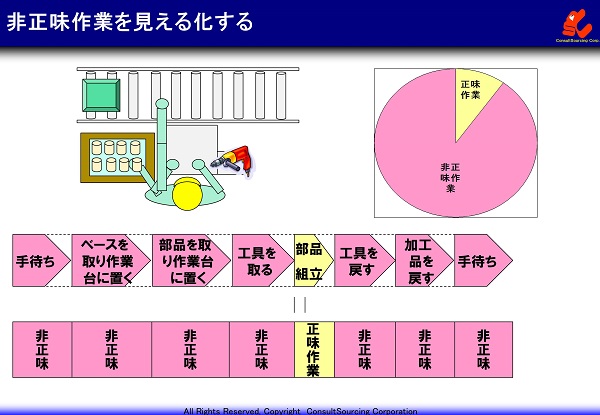
作業の流れをつくるには、人の動きを分析し、ムダを排除します。
作業者の動きを見てみましょう。
コロコンからベースを取り、収容箱から部品を取り、作業台に置きます。
工具を取り、部品組立し、工具を戻します。
加工品をコロコンに戻し、次工程に送ります。
部品組立の前後に、手待ち、置く、取る、戻す、などの動作があります。
部品組立は、正味作業であるのに対し、手待ち、置く、取る、戻す、などの動作は非正味作業です。
作業の流れを阻害するものは、このような非正味作業です。
非正味作業を減らすことで、流れのある作業が設計できます。
非正味に焦点をあてた改善をはかる
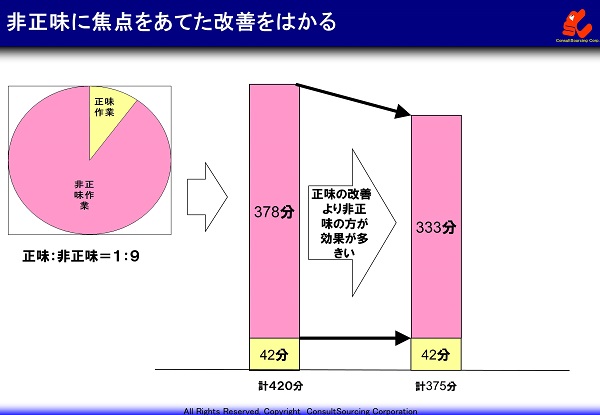
改善の対象は、非正味作業です。
先ほどの事例では、部品組立の正味作業の割合1に対し、手待ち、置く、取る、戻す、などの非正味作業の割合が9近くありました。
1日420分に換算すると正味作業42分に対し、非正味作業378分になります。
工程間のバラツキを削減する際の改善の対象は、このような非正味作業です。
正味作業に焦点を当ててしまうと、同じ10%の改善でも4分しか稼げないことになりますし、品質面などにも悪影響を与えかねません。
平準化による作業の流れ化
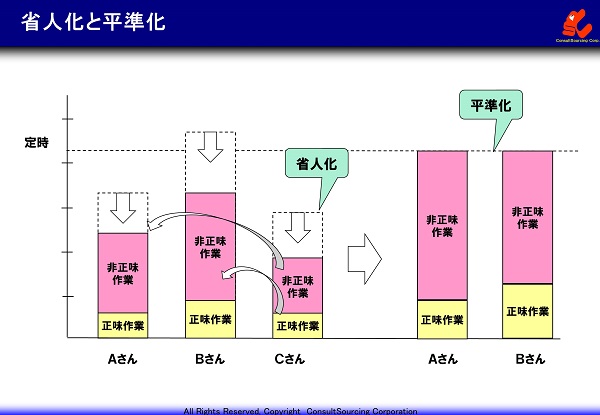
平準化による作業を流れ化します。
3人作業のバラツキから、非正味作業のムダを排除すると、1人あたりの工数は少なくなります。
そこで、3人で行っていた作業を2人でできるようにします。
これを目のある省人化と言い、作業改善や設備改善により、人をひとり単位で省くことになります。
Cさんの仕事をAさん、Bさんに割り振る際、バランスが取れるよう配分し、山の高さが揃うようにします。
これが平準化です。
リードタイムとは
工程間の在庫は、それを“停滞”と見なし、生産プロセスにおける“待ち時間”ととらえます。
◆トータル・リードタイム
トータル・リードタイムとは、調達リードタイム+生産リードタイム+物流販売リードタイムになります。
中でも、生産リードタイムは、原材料が工場に入り加工され出荷されるまでの時間を指します。
◆生産のリードタイム
受注を受け出荷されるまでの生産リードタイムは、加工時間+停滞時間で構成されます。
加工時間とは、いわゆる作業時間のことで、付加価値を生む正味作業時間と付加価値を生まない付帯作業時間(作業準備時間)に分けることができます。
停滞時間とは、加工を待っている待ち時間(作業待ち時間)のことで、ロット形成されるための待ち時間、運搬している待ち時間、手待ちとなっている待ち時間、などがあります。
生産のリードタイム=加工時間(正味作業時間+付帯作業時間)
+停滞時間(情報の停滞時間+検査時間+運搬時間+手待ち時間+・・・)
◆加工時間の短縮より停滞時間の短縮
例えば、
あるプレス工程における1枚のプレス製品をつくるための生産リードタイムを、
加工時間(1ショット10秒)+情報の停滞時間(2日)+検査時間(1分)+運搬時間(1時間)+手待ち時間(20分)と仮定します。
これを比率であらわすと、
加工時間:停滞時間=10秒:86,400秒+60秒+3,600秒+1,200秒=10:91,260=1:9,126となります。
つまり、加工時間1に対して、停滞時間の比率は9,126です。
この意味するところは、
改善の狙いどころを、加工時間の1秒を狙うより、
同じ10%改善するのであれば、停滞時間の912秒(15分)を狙えということです。
1:9,126というと、すごく多いように感じる方もいるかと思いますが、
1:数万という比率のような会社も結構あります。
停滞時間は、イコール在庫となります。
改善の狙いどころは、まずは停滞時間であり、流れをつくることで大きな効果が生まれてきます。
◆リードタイムを短縮すれば、品質が向上する
リードタイムが長くなり、そこかしこに仕掛品や完成品で在庫が膨れ上がれば、運搬や保管の際に破損や劣化が生じます。
つまり、リードタイムを短縮すれば、このような運搬や在庫のムダが削減され、品質は向上します。
リードタイム短縮の進め方
リードタイムの短縮にはいくつかの方法がありますが、ここではまず「細くて早い」流れをめざした整流化改善による短縮を紹介します。
◆リードタイムの短縮方法
リードタイムの短縮には次のような方法があります。
①整流化;前後工程での分岐・合流をなくし簡素化し、一気通貫の流れをつくる
②同期化;前後工程での生産必要数・稼動時間・生産順序を合わせる
③ライン化;設備を工程順に並べる
④1個流し;1個ずつ加工できる設備にする(大ロットから小ロット生産へ)
◆改善の原則「ECRS」
前後工程での分岐・合流をなくすことを考える場合、
「ECRS」(①無くす、②一緒にする、③順序変更、④単純化)の4つの観点から検討します。
改善効果の高い順に並んでいるので、通常上から順番に考えていきます。
①Eliminate(やめる、捨てる、除く)
例えば、A→B→C工程という3つのプロセスを経て製品が完成する場合、B工程を無くしてA→C工程というつくり方ができないか。
②Combine(統合する、結合する)
例えば、切断→塗装→接合という3つのプロセスの場合、切断した後、塗装と接合を同時行いながら切断→塗装&接合という2つのプロセスにならないか。
③Rearrange(並べ直す)、あるいはReplace(置き換える)
例えば、切断→塗装→接合という3つのプロセスの場合、塗装→切断→接合というように並べ替えることで流れができないか。
④Simplify(簡単にする、単純にする)
例えば、接合プロセスにおいて溶接をしている場合、簡単なビス止めで対応できないか。
整流化改善を進めるために改善リーダーをつくる
トヨタの整流化改善は、リードタイムを極限まで短縮することにあります。
リードタイムの短縮は、仕掛かり在庫の削減だけでなく、品質の向上、量変動への対応性の向上などがはかられ、それらによってロスコストが減り、原価低減が実現されます。
整流化改善は、セルライン化、U字ライン化によってリードタイムの短縮をめざす改善スタイルです。
このような改善を実現するためには、小ロット生産、1個流しのためのライン編成・レイアウト改善と段取り・作業改善のできる整流化改善リーダーの育成が不可欠です。
リードタイムの短縮による品質向上と量変動対応力のアップ、ロスコストの低減をめざしましょう。
トヨタ生産方式の改善に役立つツール・帳票
Copyright © 改善と人材育成のコンサルソーシング株式会社