ものづくり革新・改善の研修とコンサル
工場診断・現場診断プログラム
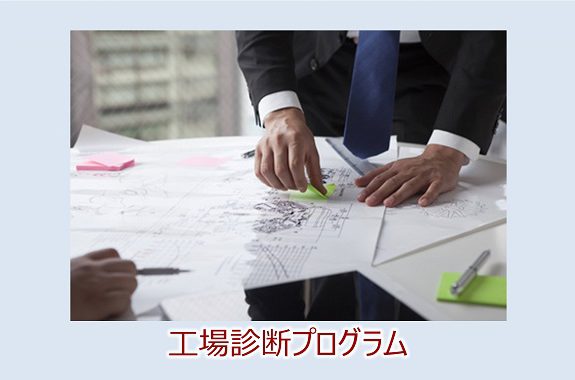
事実に基づき工場や現場の抱える課題を客観的かつ専門的に洗い出す
工場診断・現場診断は以下の目的で行います。
・工場の生産性向上のための課題の洗い出しと改善策の明確化
・改善投資判断のための改善効果の見積もり
工場診断の診断項目
・工場の5Sレベルの診断(工場内巡回による調査)
・物と情報の流れ分析(受注から生産、出荷の一連の情報と物の流れ追跡調査)
・コア・プロセスの生産性/可動率レベルの診断(設備能力・可動率調査)
・コア・プロセスの作業分析(作業観察によるムダの抽出)
・QCDパフォーマンスの診断(QCDの管理データの分析)
・要員管理のしくみの診断(要員管理業務の手順の調査)
・管理監督者の意識・管理・改善力調査(インタビュー)
・物と情報の流れ分析(受注から生産、出荷の一連の情報と物の流れ追跡調査)
・コア・プロセスの生産性/可動率レベルの診断(設備能力・可動率調査)
・コア・プロセスの作業分析(作業観察によるムダの抽出)
・QCDパフォーマンスの診断(QCDの管理データの分析)
・要員管理のしくみの診断(要員管理業務の手順の調査)
・管理監督者の意識・管理・改善力調査(インタビュー)
診断のアウトプット
・診断結果報告書(各診断項目のレベルと課題)
・診断結果を受けての改善提案書
①生産スタイルの変革を含めた課題解決のための改善案と効果見積もり
②改善活動の進め方案、根付かせる施策案
・診断結果を受けての改善提案書
①生産スタイルの変革を含めた課題解決のための改善案と効果見積もり
②改善活動の進め方案、根付かせる施策案
診断のアウトプット
日 程 | 実施項目 |
2週間前 | 診断項目計画 事前データ収集項目提示 |
2週間前~当日 | 事前データ収集(指定のデータの収集) |
診断1日目 | ブリーフツアー(工場見学) 5Sレベル調査、QCDパフォーマンス診断 物と情報の流れ調査、 要員管理のしくみ調査 生産性・可動率と作業のプレ調査分析 |
診断2日目 | ブリーフツアー(工場見学) 生産性・可動率分析、作業分析 管理監督者インタビュー 課題整理と改善仮説案立案 |
診断3日目 | データ整理と分析 課題裏付け追加調査(必要に応じて) 改善仮説案の効果見積もり |
診断1~2週間後 | 診断結果の報告と改善提案 |
工場診断のご相談・見積もりのお問い合わせ(工場診断報告書例提供中!)![]() ![]() |
Copyright © 改善と人材育成のコンサルソーシング株式会社