ものづくり革新・改善の研修とコンサル, 研修
製造現場の7つのムダ取り実践研修コース

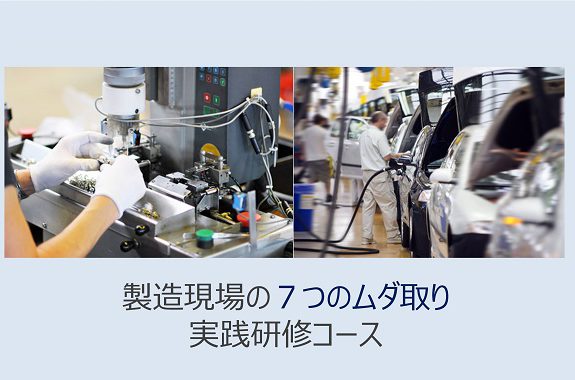
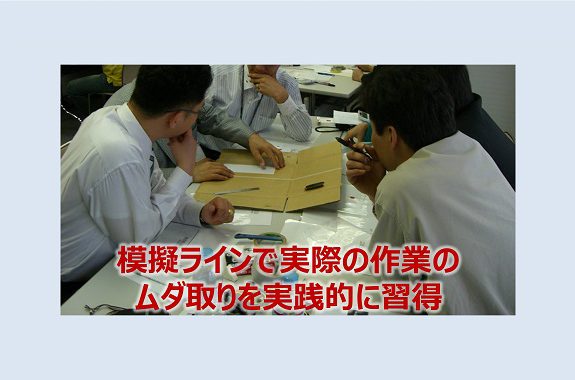

トヨタ生産方式の7つのムダ取り改善の実践力を養う
「ムダ取り」のやり方がわからない、「7つのムダ」が見えない、気づけないなどムダ取り改善がうまくできないという声が多く聞かれます。
ムダ取り改善がうまくできない職場は、ムダ探しに走り、目の前の仕事の価値や必要性を見ていないことが多く見られます。ムダとは、価値のないこと、必要のないことです。ムダ取り改善は、ムダを探すのではなく、作業や方法の意味や価値を評価し、確認することでムダが浮かび上がってきます。
本研修では、現場改善の基礎となる7つのムダ(『加工そのもの』『手待ち』『運搬』『つくり過ぎ』『在庫』『不良をつくる』『動作』)について、作業や方法を価値と必要性の視点で見て、ムダをあぶり出す改善術を習得していただきます。
模擬ラインや実作業を想定した実践演習・ゲームを通じて、体験的、実践的に学ぶことで、実務の課題解決に応える力を養います。
本研修による変化・効果について~受講者の声~
効率化や作業スピードアップをめざす改善を進めてきましたが、作業時間の短縮などの効率化の限界を感じていました。研修を通じて、作業の意味や価値を探求し、ムダな作業をやめる改善を学ぶことができ、自分たちの気づいていなかった領域があることを知ることかできました。まだまだ改善できることがあると確信しました。
【電子機器組立】
数年前、トヨタ生産方式を取り入れた工場改善を行い生産性が飛躍的に高まりまたが、近年、改善をしても効果が出ず行き詰まっていました。あらためてムダ取り改善について学んでみて、自分たちの改善方法が我流であったことがわかりました。知らぬ間に原価低減をめざして、ひたすら削る所を探す改善を繰り返していました。ムリ・ムダ・ムラの視点で必要な、価値ある作業を見極め、それら作業をどのように組み立てていくか重要であることを実感しました。削る改善からつくる改善をめざします。
コースの概要
対 象 | ・製造部門の中堅社員、リーダー、管理者、スタッフの方 ・改善活動推進担当の方、生産管理担当の方、OJT指導・インストラクターの方 ・「ムダ取り」の改善が出せなくて困っている方、新しい着眼点を取り入れたい方 |
研修形態 | 講師派遣型(オンサイト研修) |
研修時間 | 6時間×3日間 |
定 員 | 20名 |
コース構成 | 本コースには、以下の3つの研修があります。 ①加工そのもの・手待ち・運搬のムダ取り研修 ②つくり過ぎ・在庫のムダ取り研修 ③不良をつくる・動作のムダ取り研修 ※研修の構成・カリキュラムはご要望に応じてカスタマイズいたします。 |
研修1:加工そのもの・手待ち・運搬のムダ取り研修
製造現場における代表的ムダに手待ちのムダがあります。何もせず待っていることは誰が見てもムダですが、なぜ、そのような手待ちが発生したのか原因を追及すると、そこにはつくり方など方法にまつわる問題があります。つくるスピードやタイミング、組合せなどの方法のまずさが手待ちを生みます。加工そのもののムダ、運搬のムダは、一見するとムダとは思えないものにも、方法のまずさから見えないムダが潜んでいます。
本研修では、方法のまずさから発生するムダの存在に気づくための見方・捉え方、そして、ムダを取るための改善について実践演習を通じて具体的改善方法を体験的、実践的に学ぶことで、実務の課題解決力を養成します。
研修の内容
・製造現場の7つのムダにおける加工そのもの/運搬/手待ちのムダ
・4M視点で加工そのもの/運搬/手待ちのムダの抽出
・ムダを取ることによって生まれる効果
2.「加工そのもののムダ」のメカニズム
・つくるスピードを決める
・部分最適からの脱却
・ボトルネックを解消しラインバランスを整える
・工程別能力表の作成
3.「運搬のムダ」のメカニズム
・まとめてつくるとムダを生む
・集点・分点があるとムダを生む
・積み替え、載せ替えがムダを生む
・ストック型からフロー型/一個流し生産へ
・U字ライン設計/着々化
・標準作業組合せ票の作成
4.「手待ちのムダ」のメカニズム
・人を機械の番人にさせない
・標準手持ちとは
・標準作業票の作成
5.加工そのもの/運搬/手待ちのムダ削減の実践演習
【改善ゲーム】仮想工場をつくり、ムダに対する工程改善/整流化改善策を実施し、効果を測定する
研修2:つくり過ぎ・在庫のムダ取り研修
在庫そのものをムダということに抵抗を感じる方は少なくありません。適正在庫を待つことで管理が楽になる事実があるからです。
しかし、在庫は同時に現場や管理の問題を見えなくしてしまう怖さもあります。例えば、需要変動に対してズレている生産体制の問題を隠してしまい、慢性的な欠品原因に気づかせることを遅らせたりします。
つくり過ぎのムダ、在庫のムダは、それ自体はあまり問題とはなりませんが、様々な問題を見えなくしたり、解決を阻んだりします。
本研修では、つくり過ぎのムダ、在庫のムダのもつ怖さに気づき、ムダとして捉えて改善するために、実践演習を通じて具体的改善方法を体験的、実践的に学ぶことで、実務の課題解決力を養成します。
研修の内容
・製造現場の7つのムダにおけるつくり過ぎ/在庫のムダ
・4M視点でつくり過ぎ/在庫のムダの抽出
・ムダを取ることによって生まれる効果
2.「つくり過ぎのムダ」のメカニズム
・つくり過ぎが生まれる背景
・つくり過ぎから生まれる罪悪
・つくり過ぎは問題を隠してしまう
・在庫と欠品の関係の理解
・在庫と生産ロットの関係の理解
・計画生産のまずさがつくり過ぎを生む
・小ロットとリードタイム短縮へ
3.つくり過ぎのムダ削減の実践演習
【シミュレーションゲーム】欠品を起こすことなく、つくり過ぎず、在庫削減するにはどうすべきかグループワークで体験する
4.「在庫のムダ」のメカニズム
・計画押し込み生産の心理
・低コスト/高効率/安心賃主義からの脱却
・在庫削減の着眼点
・原材料削減の着眼点
・在庫を減らすことで競争力が生まれる
5.在庫のムダ削減の実践演習
【改善ゲーム】不要なものを廃棄し、必要なものをどのように管理し、維持していくかというプロセスをグループワークで体験する
研修3:不良をつくる・動作のムダ取り研修
不良品はムダであることは誰もが認識しています。しかし、本当のムダは不良品ではなく、不良品をつくる動作がムダなのです。1つの不良品が生まれたとき、その背景には数十回の危うく不良品をつくりそうになった動作があります。不良品をつくりそうになってたとき、正常な動作に比べて余分な動作が含まれます。これがムダとなります。
不良品をつくりそうになる動作を繰り返していれば、いつか必ず、不良品を作ってしまい、それが顧客に出荷されてしまったら、ムダでは済まされない信用問題となってしまいます。
本研修では、動作のまずさから発生するムダの存在に気づくための見方・捉え方、そして、ムダを取るための改善について実践演習を通じて具体的改善方法を体験的、実践的に学ぶことで、実務の課題解決力を養成します。
研修の内容
・製造現場の7つのムダにおける不良をつくる/動作のムダ
・4M視点で不良をつくる/動作のムダの抽出
・ムダを取ることによって生まれる効果
2.「不良をつくるムダ」のメカニズム
・不良をゼロにすることは容易でない
・ニンベンのついた自働化
・品質は工程でつくり込む
・異常で止まる/異常がわかる仕掛け
・インターロックとポカヨケ
・4Mが変化する時に不良が発生しやすい
・フロントローディング/コンカレント・エンジニアリング
3.「動作のムダ」のメカニズム
・ムダの削減で正味作業を高める
・ムダ取り改善のステップ
【動作分析演習】ワークサンプリング/時間観測の進め方
・バラツキや些細な動作に着目しムダに敏感になる
・ECRSの原則/動作経済の原則
・改善成果は省人化で
・標準化で誰でもできる化
4.不良をつくる/動作のムダ削減の実践演習
【改善ゲーム】不良と動作のムダがなくなれば、品質が向上し生産性も高まる。
本ゲームでは、金属模型組立作業の中で、ムダを抽出し、改善策を段ボールなどを用いてグループで実施し、品質と生産性の効果を確認する。
研修のご相談/詳細カリキュラム・見積もりのお問い合わせ![]() ![]() |
Copyright © 改善と人材育成のコンサルソーシング株式会社